1 Der Super-GAU im Motor
Headcrash. Kurz nachdem die Ventile im Motor auf die Kolbenböden geklatscht sind, macht es der Besitzer des Krades genauso: Er klatscht seinen Hut auf die Erde und beginnt, ihn mit den Stiefeln kalt zu verformen. Wir zeigen in diesem Artikel, wie man nach einem solchen Super-GAU im Zylinderkopf aufräumt, neue Ventile einbaut und einschleift. Fotomodell ist in hier ein alter GPZ-Vierzylinder, dessen Nockenwellenräder falsch montiert waren.
Solcherlei Kopfschmerzen kommen auch bei Autos immer wieder vor. Schuld ist dann allermeistens ein gerissener Zahnriemen, dessen Wechselintervall gnadenlos überdehnt wurde. Allerdings reißen auch Steuerketten; alternativ gehen Spanner kaputt und Kette oder Riemen rutschen lustig über die Räder.
Der Effekt ist in allen Fällen derselbe. Wenn man jedoch ganz großen Dusel hat, baut der Kopf des Motors so, dass die Ventile genug Platz haben und nicht auf die Kolben aufsetzen. Oder man hat einen Ein- oder Zweizylinder, bei dem die Nockenwelle stehen bleibt, wenn die Ventile nicht betätigt sind.
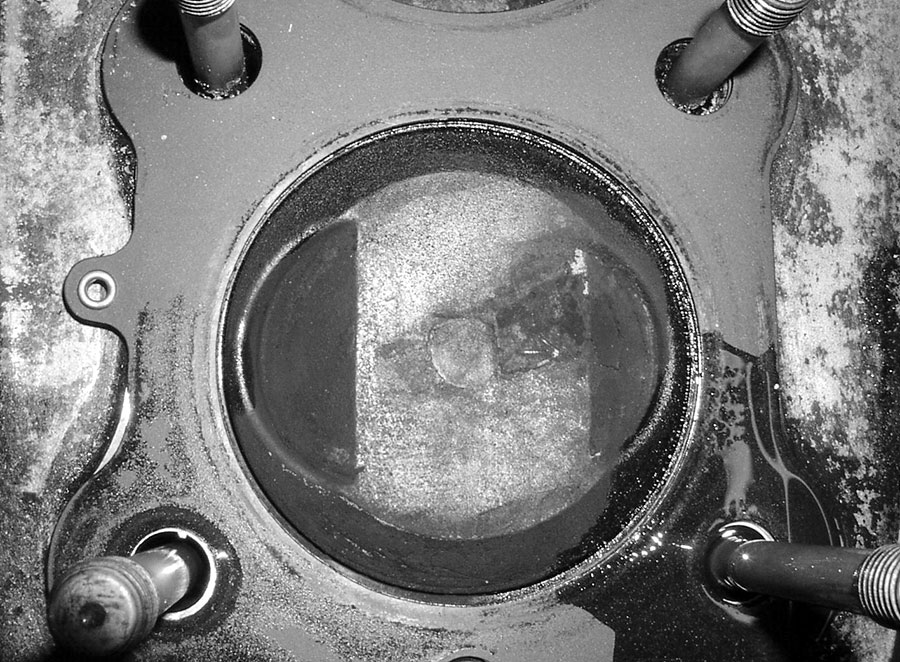
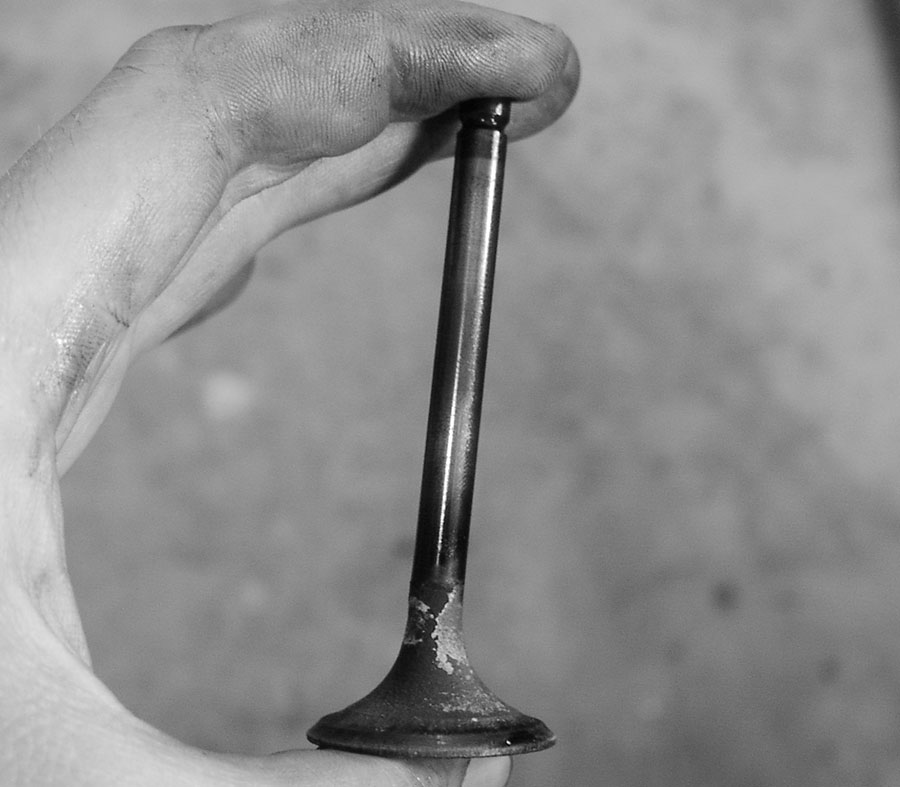
2 Original oder Nachbau?
Ventile als Originalersatzteile sind ziemlich teuer. Als Nachbauten kosten sie meistens nicht mal die Hälfte. Beim Einkaufsbummel auch an Ventilschaftdichtung und Kopfdichtung denken. Am billigsten kommt man oft mit einem Motordichtsatz aus dem Zubehörhandel weg – da ist dann bis auf Wellendichtringe alles drin, was man braucht, um die Kiste wieder zuzukriegen.
Häufig zu einem Preis, für den man beim Vertragshändler nicht mal eine Kopfdichtung bekommt. Ist der Zylinderkopf nicht wie hier mit Stehbolzen, sondern mit Dehnschrauben festgezurrt, muss man die auch ersetzen.
3 Der Schaden aus der Nähe
Hat man den Zylinderkopf runter, kann man sich den Schaden in aller Ruhe besehen und erst mal alles saubermachen. Reste der Kopfdichtung abkratzen und Ölkohle aus dem Brennraum popeln.
,
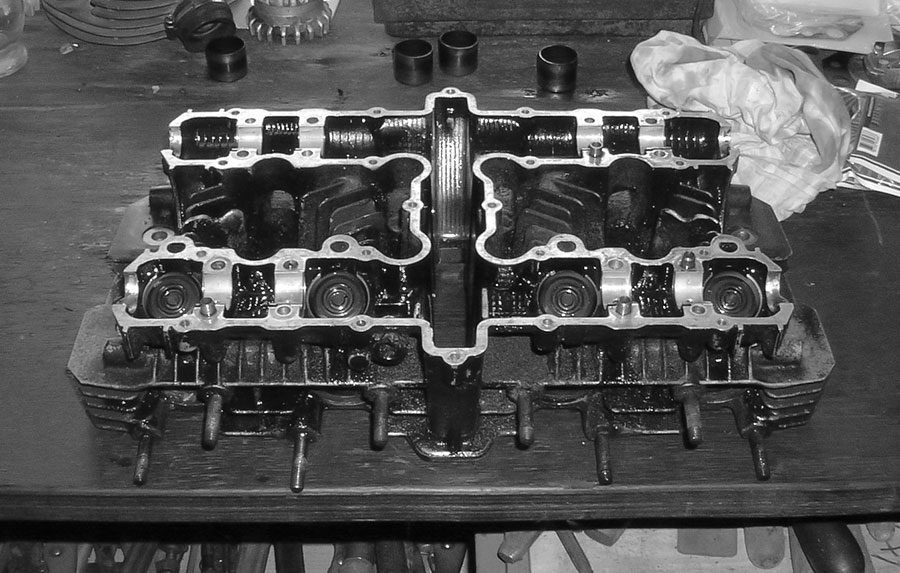
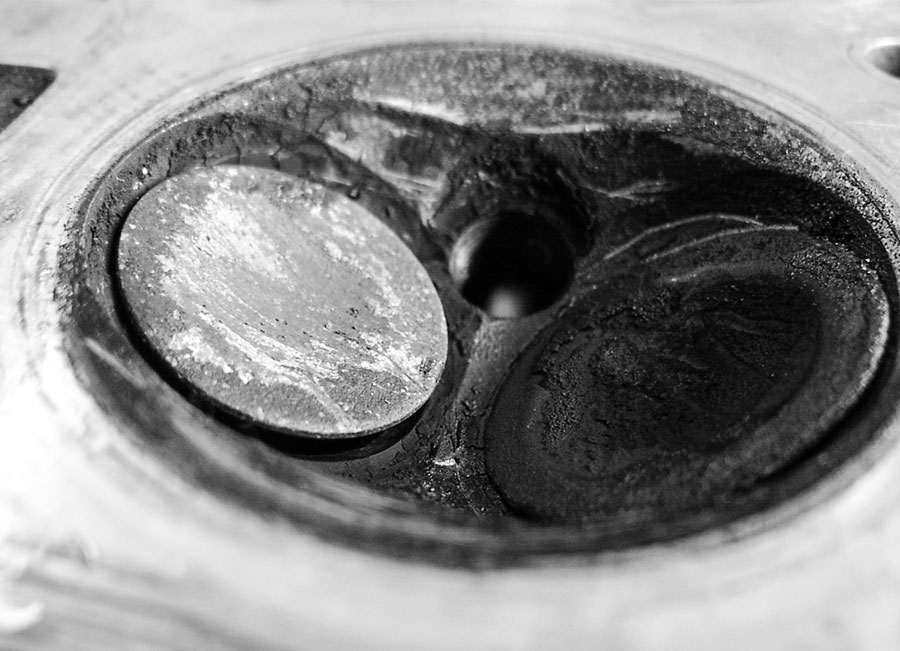
4 Tassenstößel
Bevor man anfängt, den Federteller runterzuruppen, muss alles, was an Ventiltrieb noch im Weg ist, abgebaut werden. Bei dieser GPZ sind es die Tassenstößel, mit denen das Spiel eingestellt wird.
Die Dinger sitzen saugend-schmatzend im Kopf und beherbergen untendrunter die Shims, mit denen man das Ventilspiel einstellt. Bei anderen Motoren ist die Nockenwelle selbst im Weg oder die Kipphebel. Das alles muss raus, bevor man sich an die Ventile macht.
Wichtig: Alle Teile des Ventiltriebs, also auch die Stößeltassen und Shims fein säuberlich paarig oder nummeriert zu Ventil und Federn aufbewahren. Spart später mühsames Ventileinstellen.
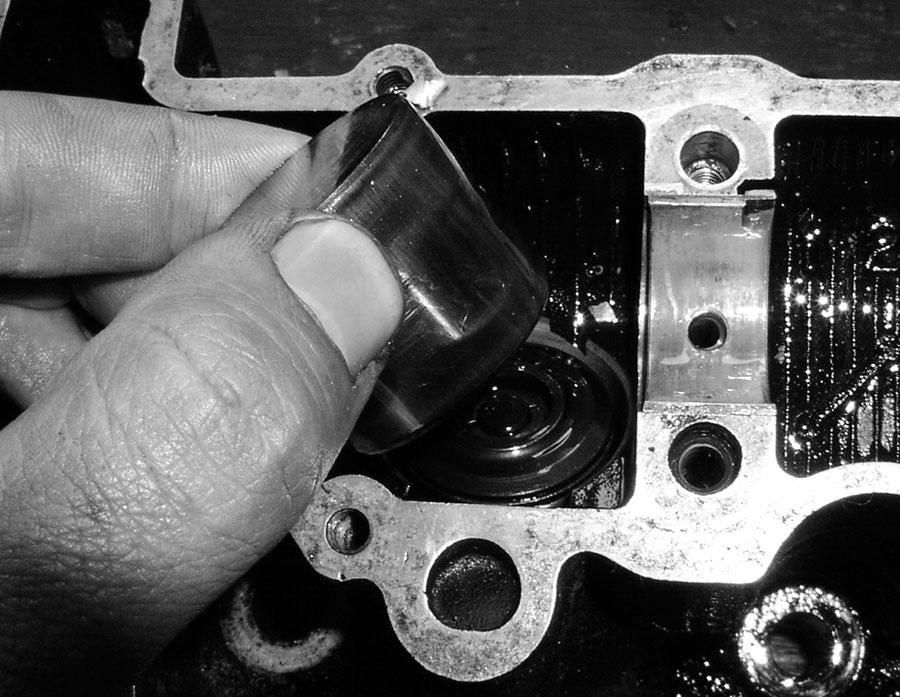
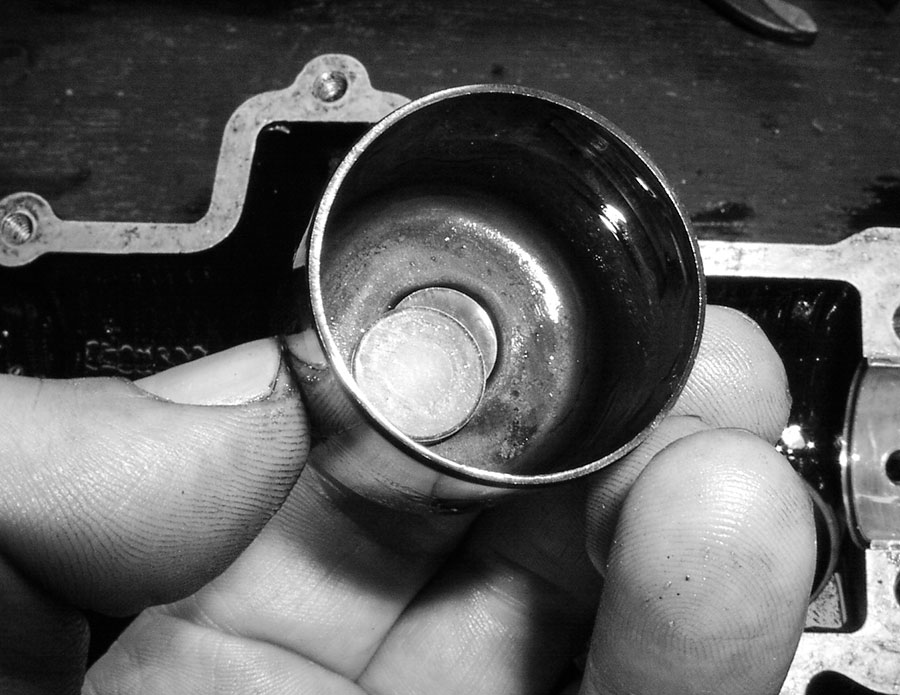
5 Ventil-Werkzeug
Um die Ventile auszubauen, braucht man Spezialwerkzeug, das man sich aber in aller Regel auch selber bauen kann. Kern des Spezialwerkzeugs ist eine schnöde Schraubzwinge, mit der man etwas tiefer spannen kann. Zusätzlich braucht man eine Hülse, mit der man den Federteller des Ventils runterdrücken kann.
Als Ausgangsmaterial nimmt man ein Stück Rohr, das man mit Winkelschleifer und Feile solange bearbeitet, bis es passt. Will man es ganz fein haben, kann man auch noch eine Platte obendraufschweißen, damit die Zwinge besser hält.
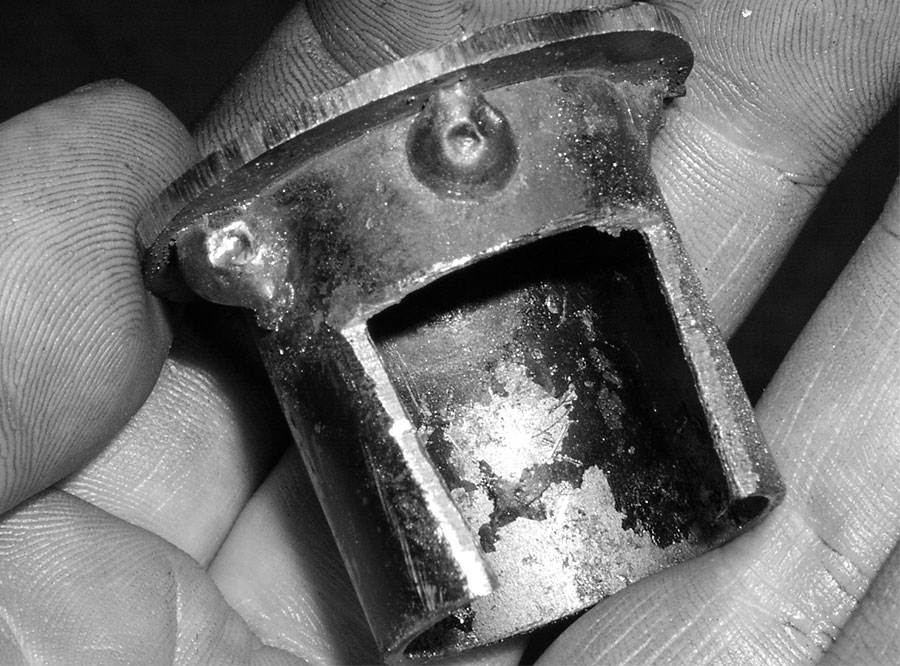
6 Zwinge spannen
Man braucht für die Demontage der Ventile neben Zwinge und Hülse vor allem eine stabile Werkbank und ein paar Holzkeile. Die schiebt man so unter den Zylinderkopf, dass er schräg steht und man mit Zwinge unter den Ventilteller fassen kann. Die Hülse setzt man so auf den Federteller, dass man in dem Fensterchen beide Ventilkeile sehen kann.
Jetzt muss man das ganze möglichst gerade zusammenspannen, damit einem die ganze Suppe nicht von der Werkbank rutscht. Wenn es beim Spannen irgendwann „knuck“ macht, sind die Keile freigekommen. Jetzt noch ein wenig weiterdrehen, damit die Dinger noch ein wenig weiter herausstehen.
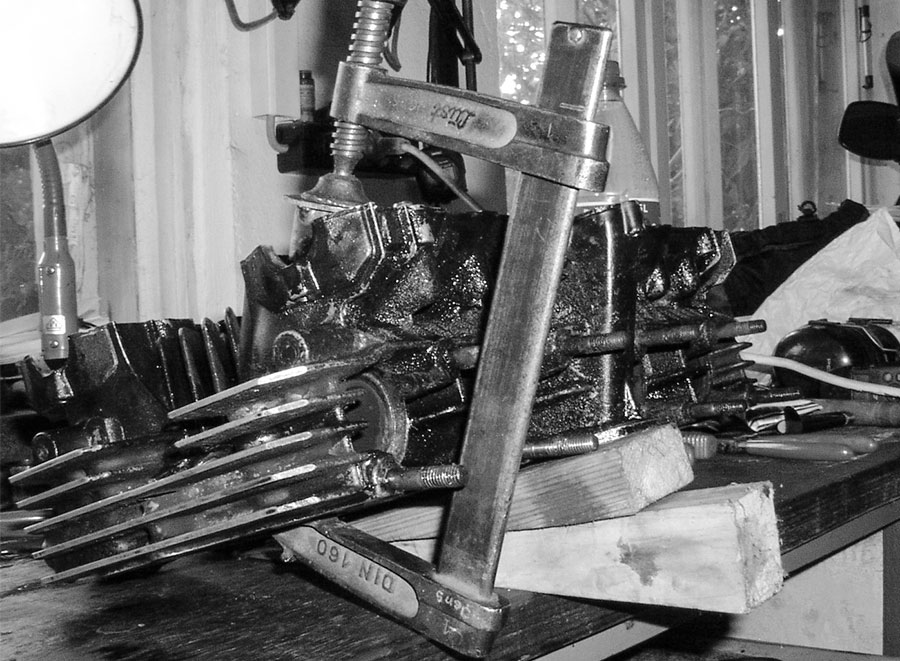
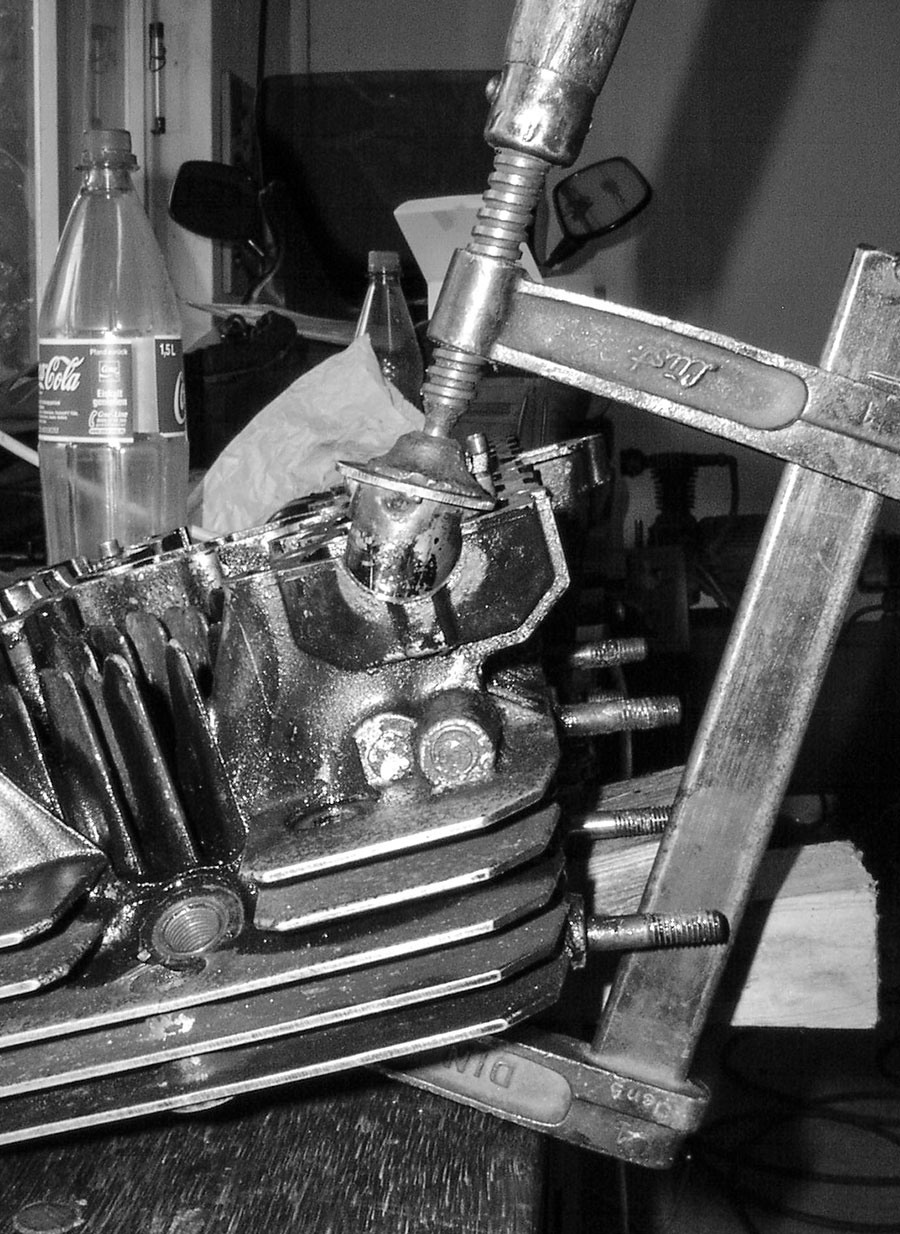
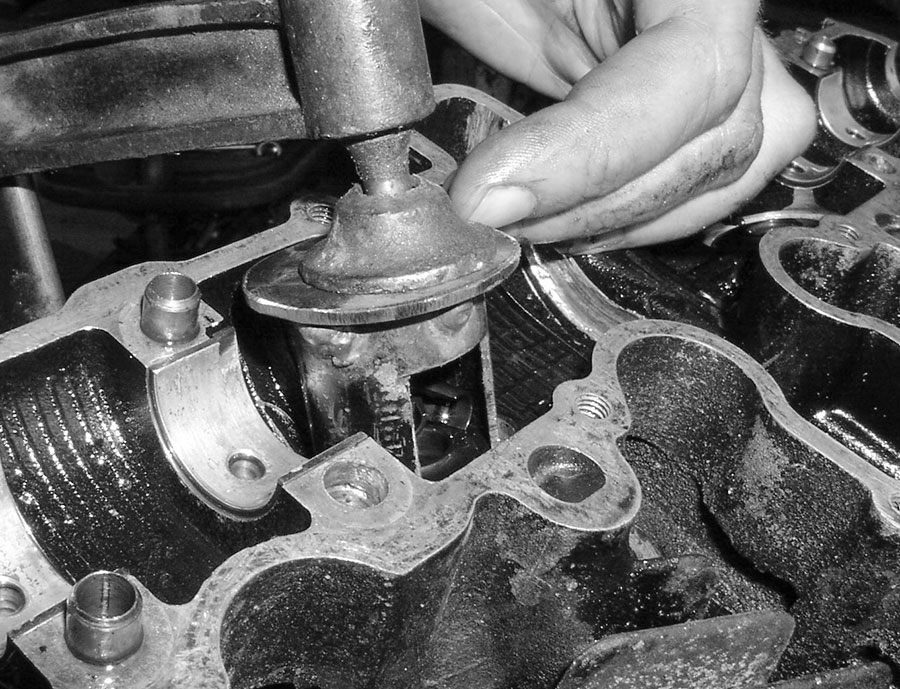
Letzte Aktualisierung am 2024-04-03 / Affiliate Links / Bilder von der Amazon Product Advertising API
7 Ventiltrieb zerlegen
Die Ventile werden von der oder den Ventilfedern auf ihren Sitz gepresst. Die Kraft dazu wird vom Ventilfederteller übertragen. Der ist mit kleinen Keilen, die in Ringnuten im Ventilschaft greifen, am Ventil befestigt.
Diese Ventilkeile müssen raus, damit man den Federteller, die Federn und schließlich das Ventil rausziehen kann.
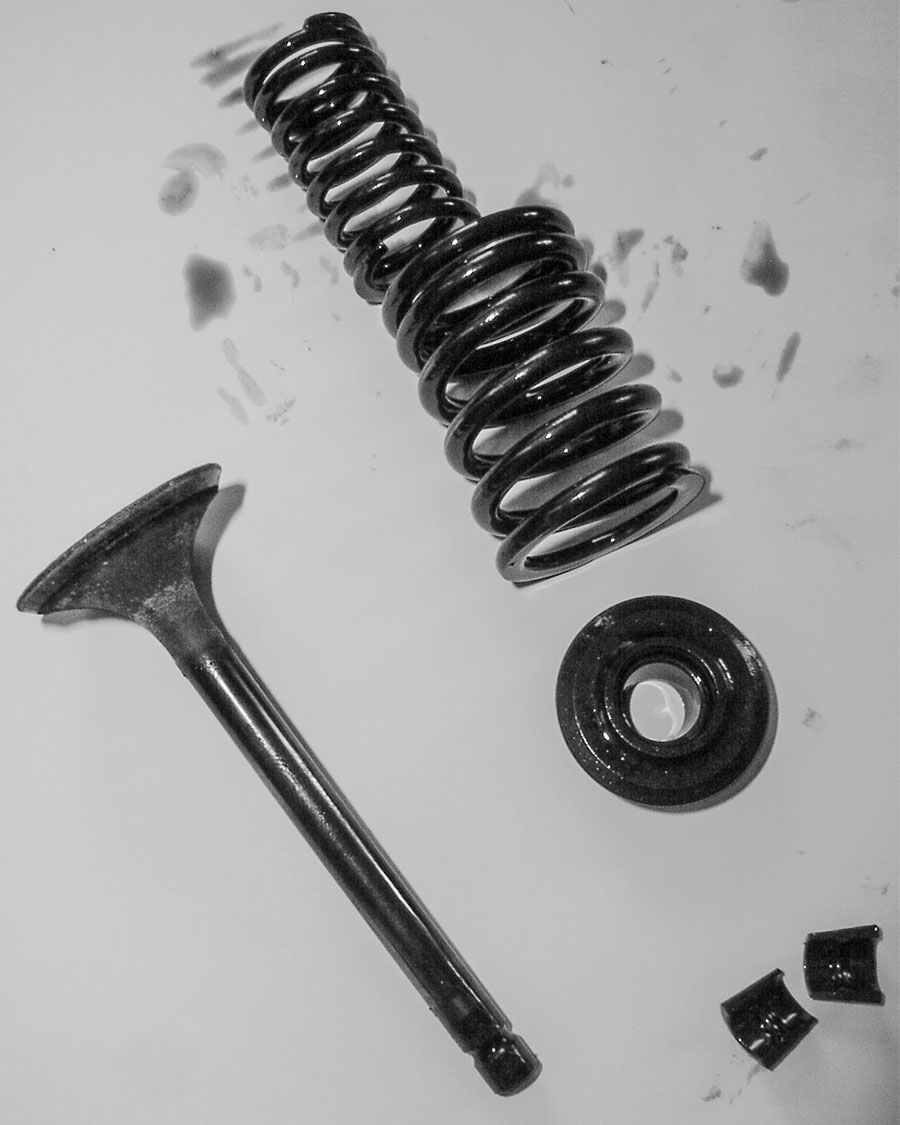
8 Ventilkeile rausnehmen
Mit einer Pinzette lassen sich die Ventilkeile am besten herausfischen. Man kann sein Glück auch mit einem Stückchen Draht oder einer Radiozange versuchen. Das kann man allerdings auch verfluchen, wenn einem ein solcher mikroskopischer Keil in den Unratdschungel unter der Werkbank geflitscht ist: Es gibt Leute, die Kippen dreiviertelvolle Mülltonnen aus und sieben deren Inhalt fünf Stunden lang, um die
verflochten Keile wiederzufinden.
Wenn die Keile jedoch gut aufgehoben und verlustsicher auf der Werkbank liegen, entspannt man die Schraubzwinge. Federn, Federteller und Ventile hebt man mit allen Teilen des Ventiltriebs pro Ventil separat auf. Diese separate, am besten nummerierte Aufbewahrung ist wichtig: Je länger die Mühle in Betrieb war, desto deutlicher haben sich Ventilteller, Ventilschaft und Ventilsitz aufeinander eingearbeitet. Vertauscht man die Teile untereinander, bedeutet das erhöhten Verschleiß oder Undichtigkeiten.
Liegen alle Einzelteile auf dem Teller, kann man auch prüfen, ob die Ventilfedern noch die Kraft der zwei Herzen haben. Mit der Zeit werden Ventilfedern nämlich müde und schließen nicht mehr so schnell. Bei hohen Drehzahlen funktioniert dann der Gaswechsel nicht mehr 100%ig und bedeutet Verlust und Minderleistung. Mit einem Messschieber kann man die Länge der entspannten Feder mit einer frischen Feder oder dem Datenblatt des Motors vergleichen.
Ob die GPZ je wieder läuft und wie man die Ventile der Mühle einschleift, zeigt der zweite Teil dieses Artikels („Sitz“).
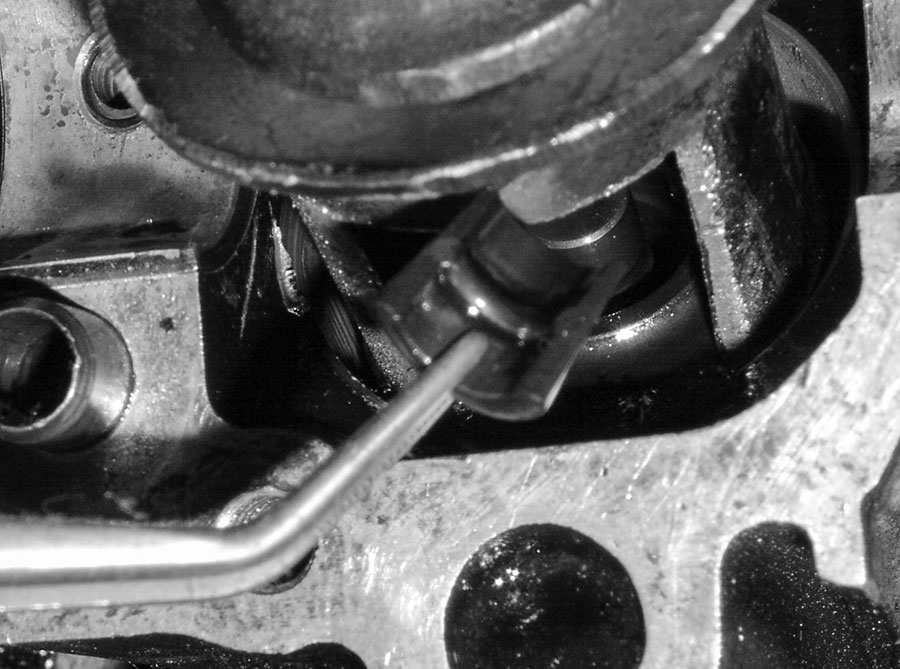
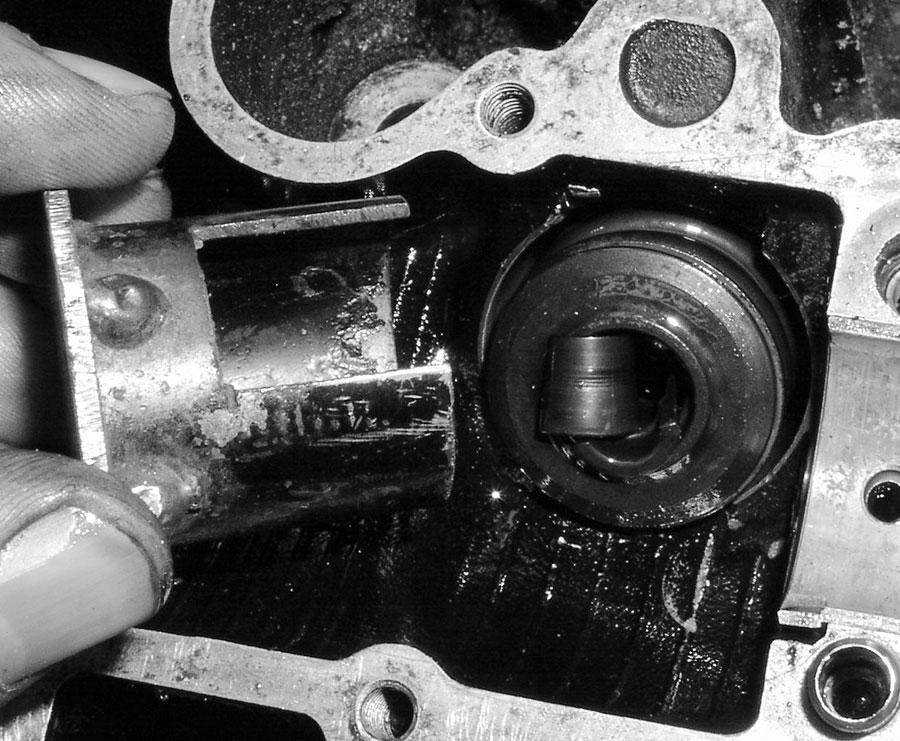
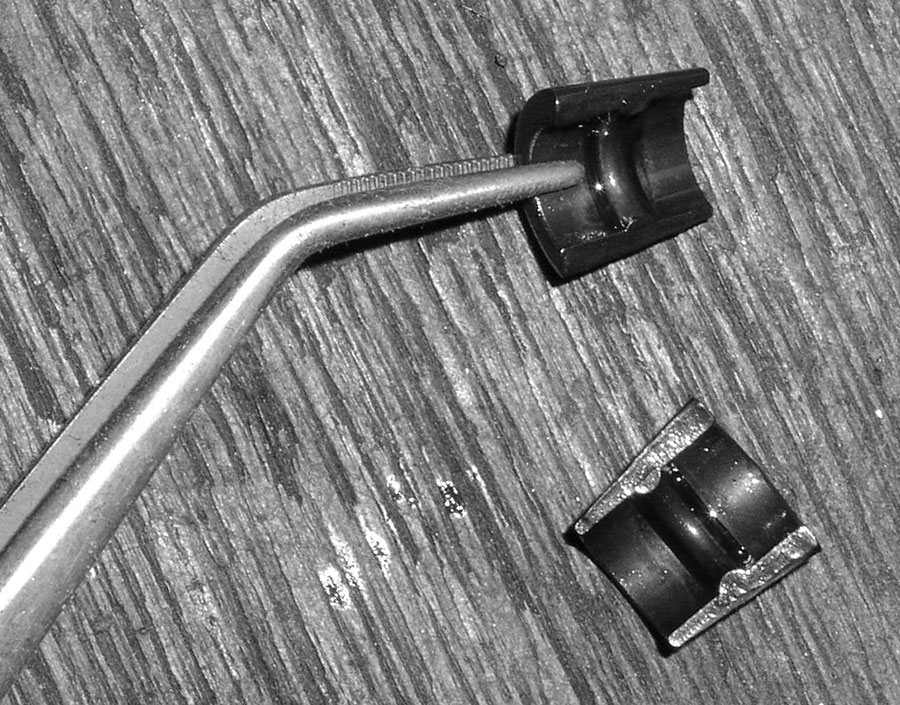
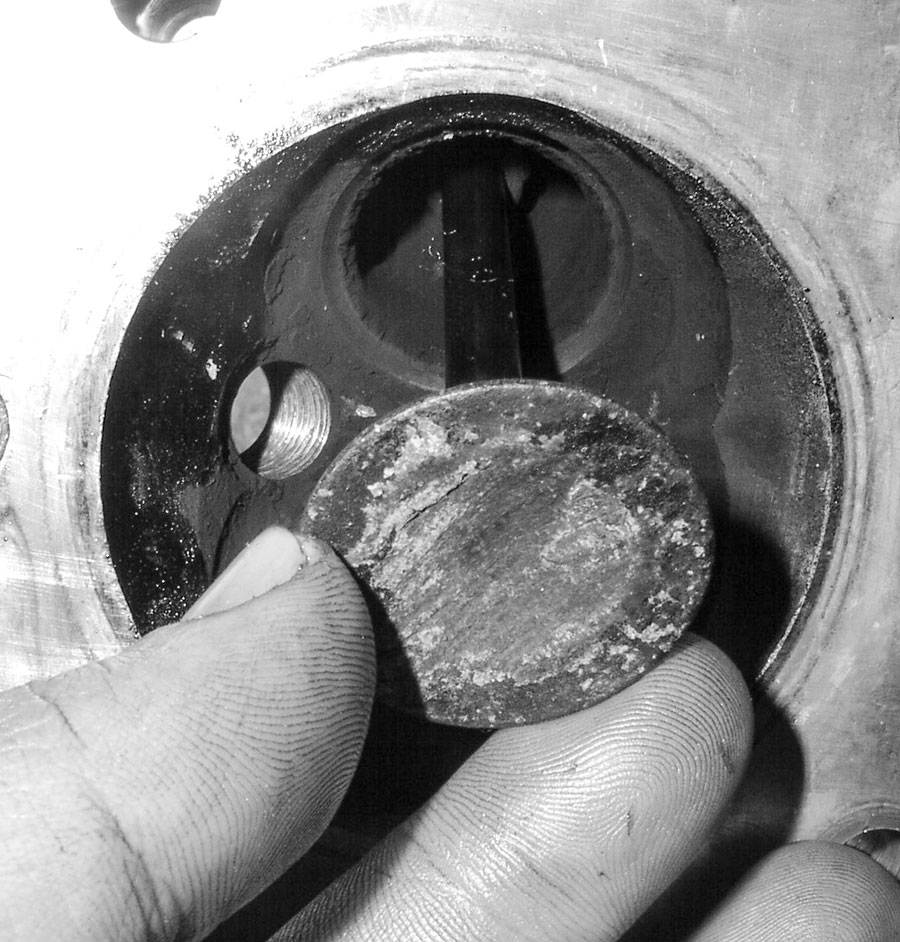
Letzte Aktualisierung am 2024-04-05 / Affiliate Links / Bilder von der Amazon Product Advertising API