Innengewinde schneiden
Ist das Kernloch endlich fachgerecht im Werkstück verankert (beispielsweise der sinnfreien Bohrplatte), sollte noch eine Fase angesenkt werden, die den Gewindebohrer zentriert und das Gewinde gratfrei macht. Im Anschluss daran wird der erste der drei Bohrer in das Kernloch geschraubt. Zack! Dabei sollte man verschiedenes im Auge haben. Zuvörderst ist wichtig, dass die Gewindebohrung grade, d.h. lotrecht auf dem Werkstück steht.
Das klingt banal, ist aber nicht so einfach, weil Schieflage menschlich ist. Und schon eine kleine Schieflage bedeutet, dass die Bohrung möglicherweise um zwei oder drei Grad aus dem Kurs geht. Mag das für die spätere Bedeutung der Bohrung egal sein, so sorgt diese Kursabweichung schon nach wenigen Umdrehungen des Windeisens für deutlichen Widerstand, weil sich der Bohrer verkantet.
Das Ding frisst sich nämlich brav Windung um Windung ins Material und wird dabei gehörig verspannt. Hat man Glück, so kuckt der Bohrer nachher unten aus dem Loch heraus und hat nur das Gewinde aus dem Kurs gebracht. Mit etwas Pech tut es aber ein trockenes „knack“, weil sich der Bohrer auf wundersame Weise in zwei Stücke teilte.
Diese Zweiteilung ist ganz und gar unschön, einfach weil das Herausfummeln abgebrochener Gewindebohrer-Fragmente Zeit frisst oder mitunter gar nicht geht.
Um diesen GAU zu verhindern, sollte man schon während des Gewindeschneidens einen schnöden Taschenwinkel in Anschlag bringen. Mit diesem Ding lässt sich sicher kontrollieren, ob das Gewinde auch wirklich lotrecht sitzt – wenn nicht, muss schleunigst korrigiert oder sogar neu angesetzt werden.
Insbesondere bei Maschinengewindebohrern ist dieses lotrechte Reinfiedeln extrem wichtig: Hier wird schon ab dem 4 Gang „fertiggeschnitten“ – eine nachträgliche Korrektur der Achse ist beinahe unmöglich.
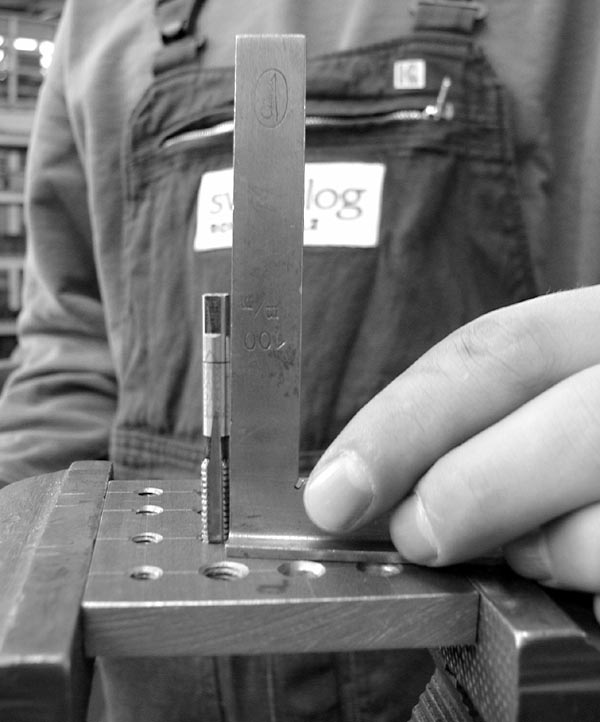
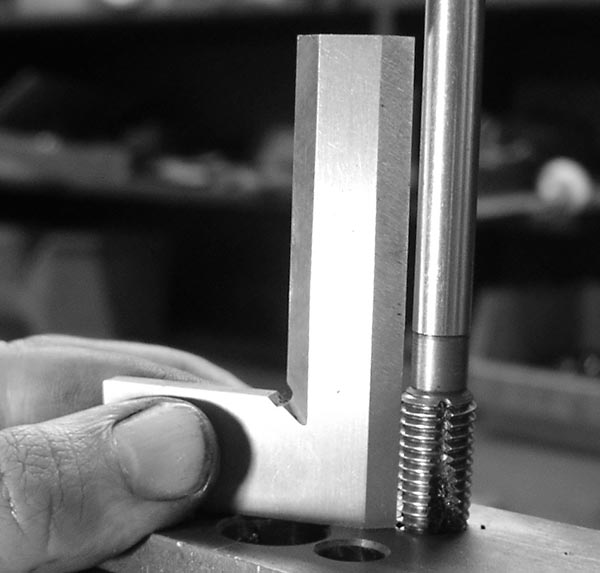
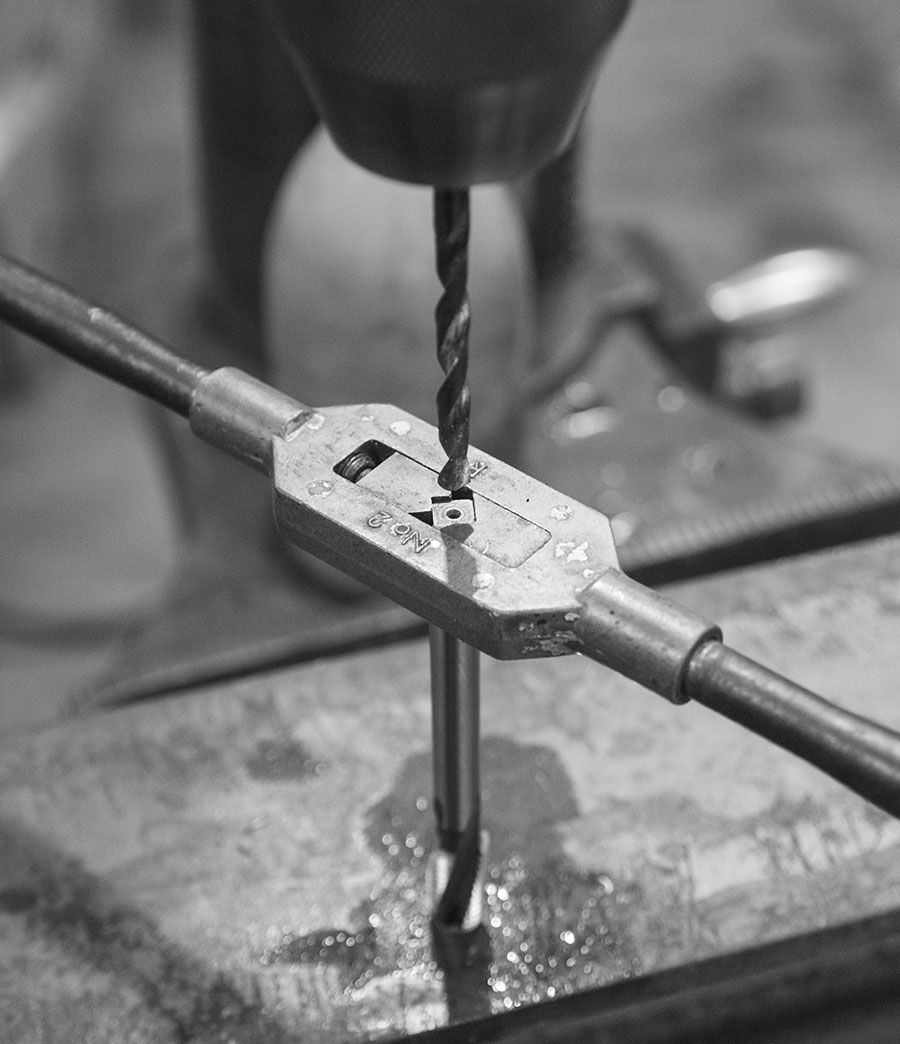
Letzte Aktualisierung am 2024-04-05 / Affiliate Links / Bilder von der Amazon Product Advertising API
Geschmierter Dreh zurück
Schmieren und Salben hilft nicht nur in Bonn, Berlin und Brüssel auf der Karriereleiter, sondern auch beim Gewindeschneiden. Welches ölige Schmierzeug hier zum Einsatz kommt, ist fast einerlei – das Zeug soll die Reibung an den Gewindeflanken herabsetzen. Neben den speziell fürs Gewindeschneiden entwickelten Schneidenölen tut es in der Werkstattpraxis deswegen auch normales Motor- oder Getriebeöl.
Während sich M8 oder M10 auch ohne Schmierung ganz passabel schneiden lassen, so steigt die erforderliche Schnittkraft / das erforderliche Drehmoment am Windeisen mit jedem Millimeter Außendurchmesser quadratisch an. Ein nicht sonderlich aufregendes M24 auf einen Bolzen zu schneiden erfordert daher bereits russische Urkraft am Hebel und lässt die Spänchen gut spuckheiß auf den Werkstattboden prasseln.
Üblicherweise geht die Gewinde-Fabrikation jedoch unspektakulär von sich: Ein paar Tropfen Schneidöl in die Bohrung träufeln und rein mit dem Gewinde-Ahl. Nach wenigen Umdrehungen mit konstantem Dreh geht es jedoch trotzdem schwer – und das liegt an der Form der Spannuten im Gewindebohrer.
Im Gegensatz zum Kollegen Spiralbohrer sind dessen Spannuten nämlich gerade. Und das sorgt dafür, dass die Späne nicht abfließen, sondern bestenfalls nach unten in die Bohrung fallen. Im ärgsten Fall backen sie einfach fest und vermackeln die eben kunstvoll geschnittenen Zähnchen.
Um das zu verhindern, kommen auf drei oder vier Vorwärts-Umdrehungen mindestens eine Viertel- oder halbe Rückwärts-umdrehung. Die bricht dann den entstandenen Span, das spürt man beim Drehen ganz deutlich. Weiterdrehen, drehen, drehen und dann wieder einen Tangoschritt zurück.
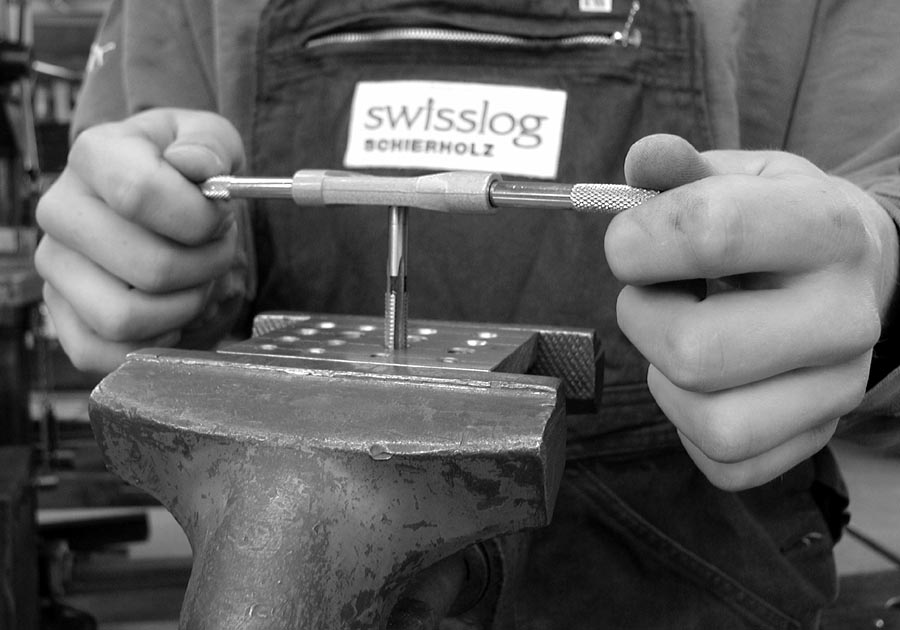
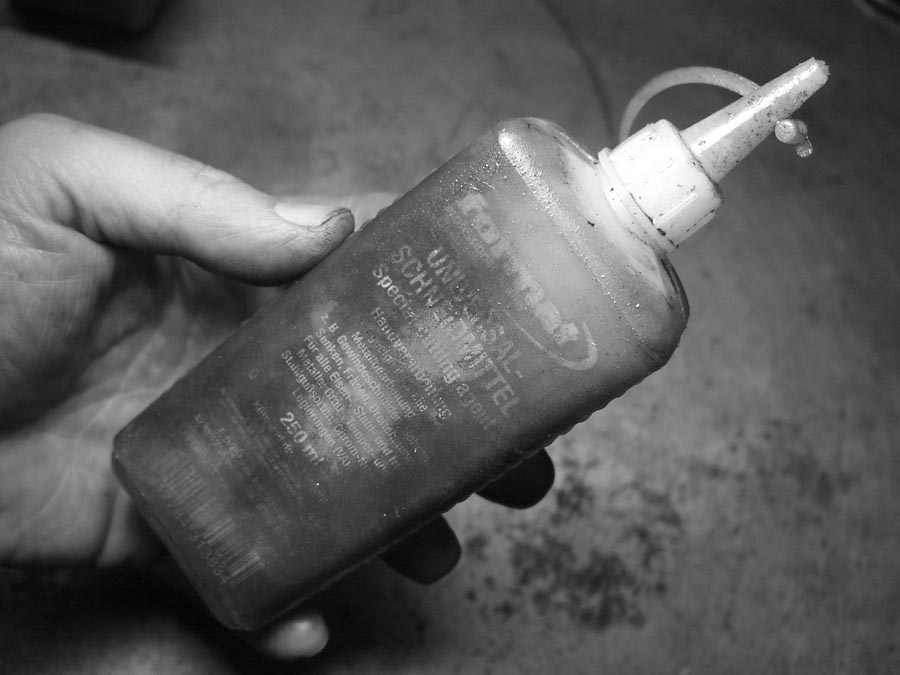
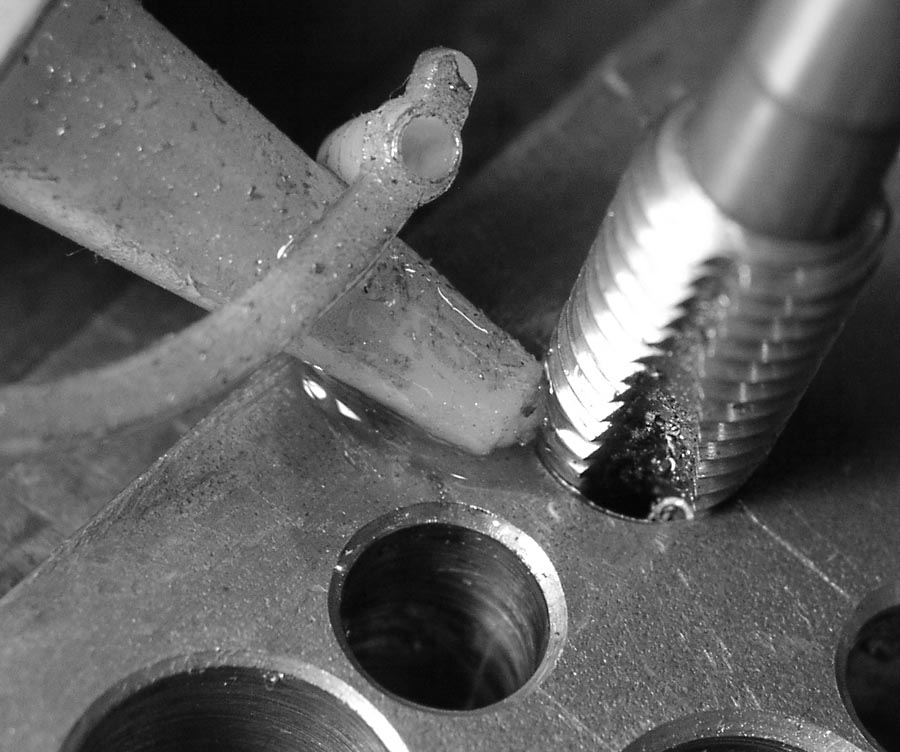