Reibung statt Zugkraft
Nochmal zurück zur grauen Theorie: Wirkt eine Drehkraft (Guido Westerwelle im Seil oder der schwitzender Schrauber mit Verlängerung an der Knarre) auf die Schraube, so erzeugt das eine Zugkraft in der Schraube. Diese Zugkraft ist THEORETISCH umso größer, je länger der Hebel, je größer die Kraft am Hebel und je kleiner die Gewindesteigung der Schraube. Das „theoretisch“ im vorigen Satz ist enorm wichtig: Denn in der Praxis kommt nämlich noch Reibung ins Spiel.
Und diese Reibung frisst immer und unter allen Umständen mehr oder weniger große Teile der herrlichen Drehkraft auf. Sie verhindert, dass das Gekurbel am Knarrengriff zu 100% in das Zusammenpressen von Zylinderkopf und Kurbelgehäuse fließt. Der Happen vom Drehmomentkuchen ist dabei sehr unterschiedlich groß: Eine eingelaufene und gut geölte Schraube erzeugt bei gleichem Drehmoment an der Zylinderkopfdichtung viel mehr Klemmkraft als ein gilbiges Exemplar, bei dem die Hälfte der Energie für das Überwinden der Rostschicht draufgeht.
Und erst wenn man diese Reibung mit in die Rechnung einbezieht, kommt das Drehmoment in der Praxis an: Die Zugkraft in der Schraube ist IN DER PRAXIS umso größer, je länger der Hebel, je mehr Kraft am Hebel, je kleiner die Gewindesteigung und je kleiner die Reibung ist. Helau!
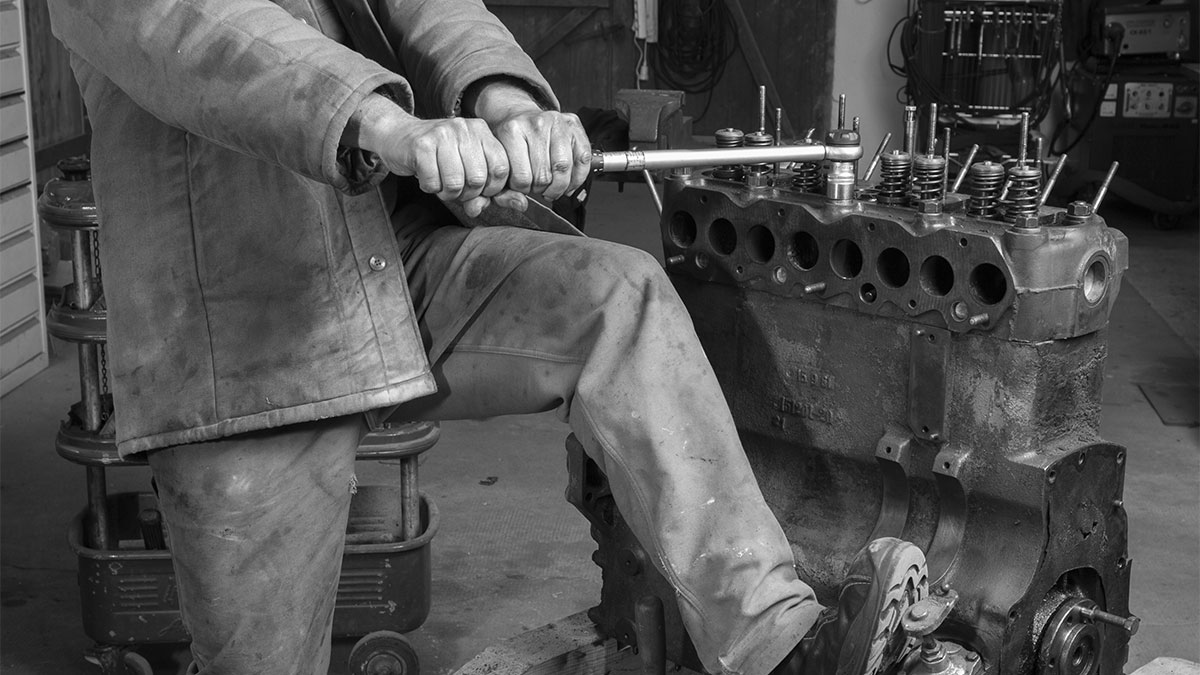
Klemmkraft, geschmiert
Und hier muss man nochmal ganz genau hinkucken: Reibung gibt’s gleich mehrfach: Reibung im Gewinde, Reibung zwischen Unterlegscheibe und Schraubenkopf und Reibung zwischen Unterlegscheibe und Zylinderkopf. Alle diese Reibkräfte addieren sich und behindern den munteren Dreh am Schlüssel. Die aufaddierte Reibung ist üblicherweise erheblich größer als die für das Spannen der Schraube erforderliche Kraft. Vor allem nimmt die Reibung zu, je mehr man die Schraube spannt. Andersherum nimmt die Reibung deutlich ab, wenn man mit der Ölkanne am Gewinde herumplempert.
Wie in dem Diagramm zu sehen, verändern bereits geringste Mengen Schmiermittel die Reib-Beiwerte der Schraubenverbindung. Diese schlichte Wahrheit kann man gar nicht häufig genug wiederholen – wird sie doch selbst in hochbezahlten Innungs-Ober-Meisterwerkstätten oft mit Füßen getreten: Geschmierte Verbindungen verhalten sich anders als trockene. GANZ ANDERS.
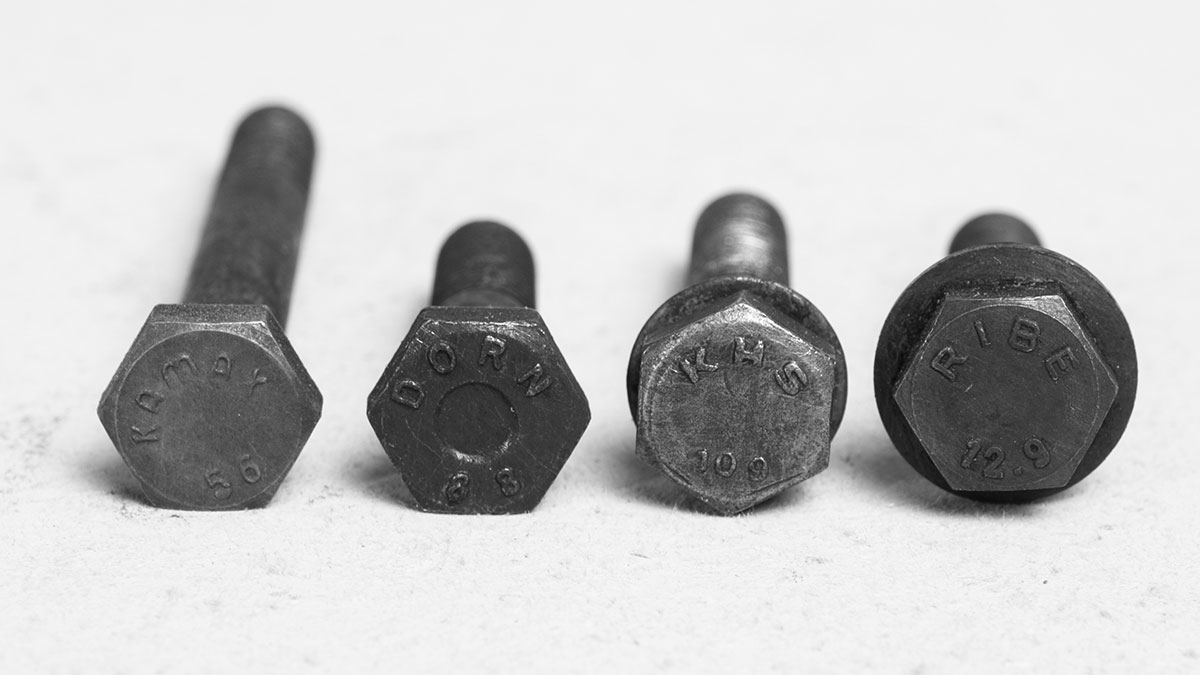
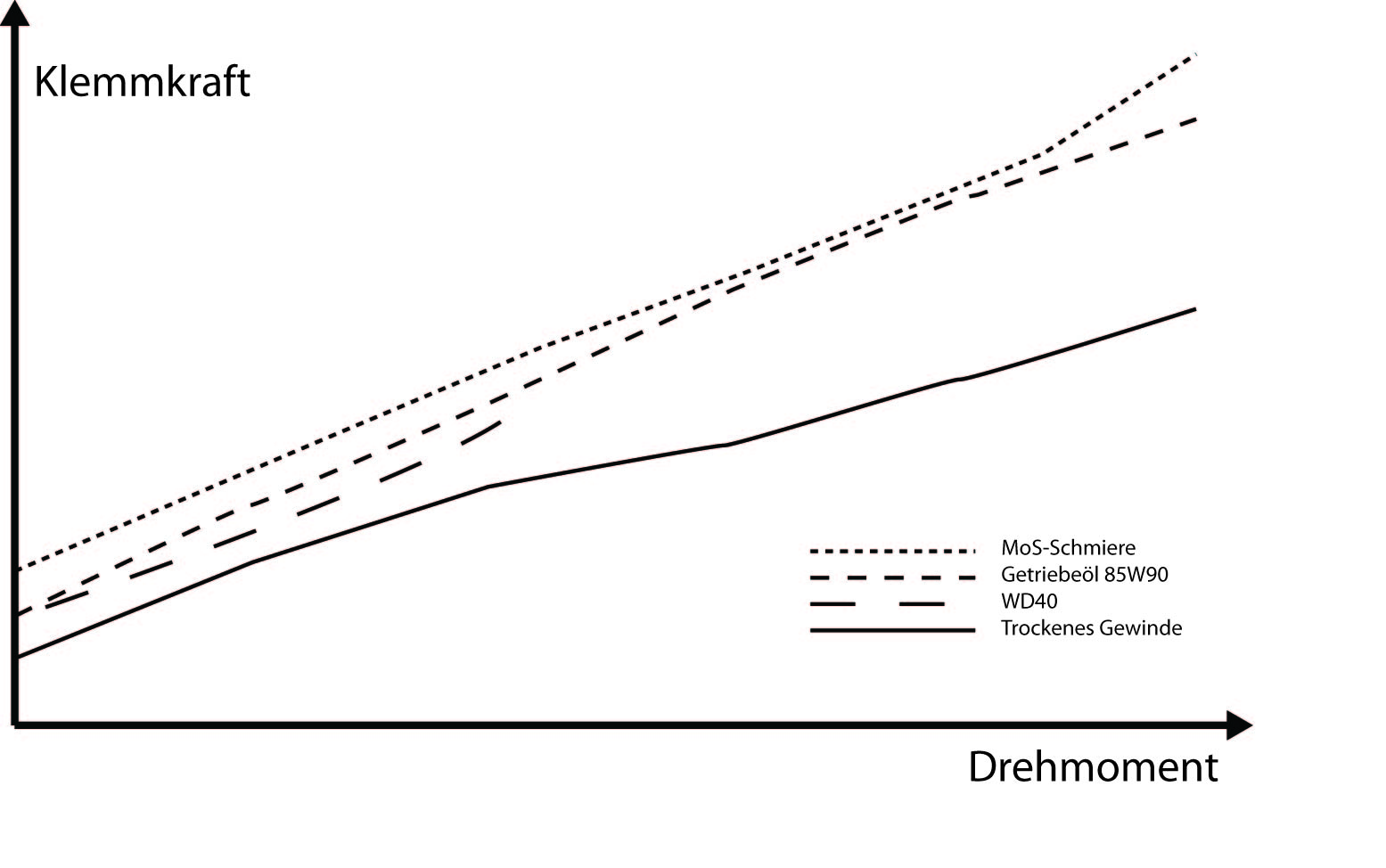
Drehmoment-Prüfstand
Wir haben das an einer M8-Schraubenverbindung einfach mal ausprobiert: Als Messinstrument diente in diesem Aufbau eine chinesische Kofferwaage von Aldi, die aber ganz brauchbar bis 50 Kilo (also rund 500 Newton) anzeigt. Um die spiddelige Schraube ein wenig zu belasten, haben wir die Kraft reichlich mit dem Messbalken übersetzt – und konnten unterm Strich bis 100 Nm auf die Schraube kriegen. In der Reihe haben wir verschiedene Schrauben, verschiedene Unterlegscheiben und vor allem zahlreiche Schmiermittel an Gewinde und Schraubenkopf getestet. Die „Ausgangs-Verbindung“ war eine in Bremsenreiniger gebadete und saubergebürstete, trockene, neue Schraube.
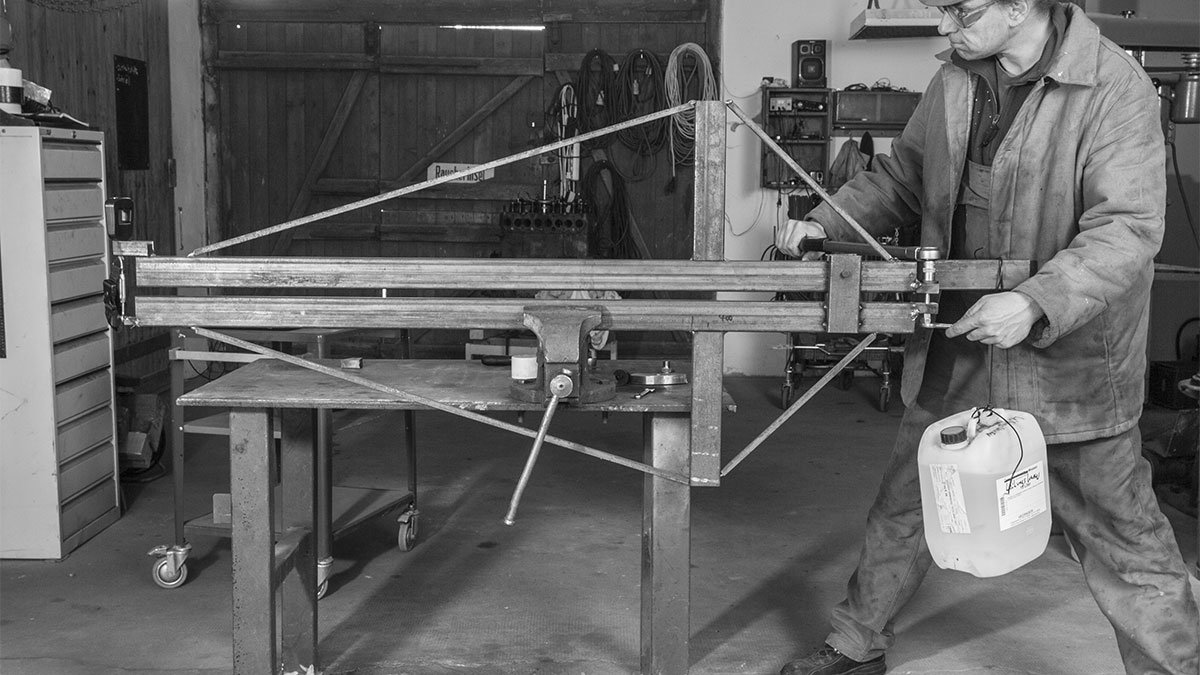
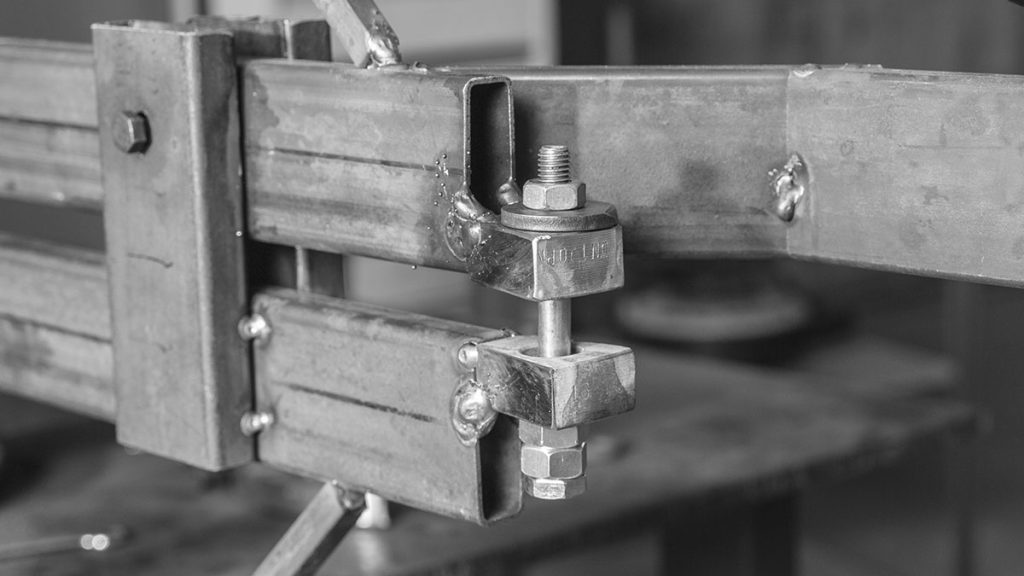
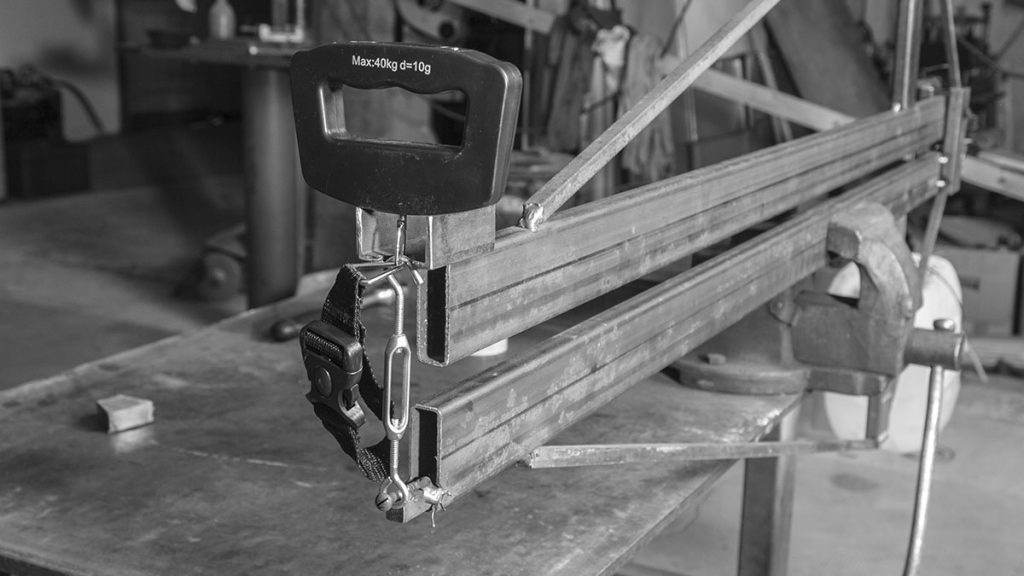
Einfluss aufs Drehmoment
In einer kleinen Messreihe zeigt sich: Die Klemmkraft der Schraubenverbindung hängt von zahlreichen Faktoren ab; das Drehmoment am Kopf von Schraube oder Mutter ist dabei prinzipiell gar nicht so wichtig. Neben der Herstellart des Gewindes (geschnitten/gerollt) hat zum Beispiel das Material erheblichen Einfluss. So verhalten sich Edelstahlschrauben völlig anders als Exemplare aus niedrig legiertem Stahl. Das betrifft auch Unterlegscheiben – montiert man eine Spannmutter auf einem dünnem Kupferring, so hat dieser nicht nur eine völlig andere Auflagefläche, sondern auch einen anderen Reibfaktor als eine breite Stahlscheibe.
Wurde das Gewinde häufiger bewegt, sind die Flanken aufeinander eingearbeitet und laufen „besser“, d.h. sie bieten weniger Widerstand – und können den Drehmomentwert um über 10 Prozent verfälschen. Noch besser laufen Gewinde, wenn man sie schmiert, salbt und ölt. Dabei verhalten sich unterschiedliche Schmierstoffe am Gewinde ganz verschieden, wie ein Test am Drehmoment-Balken zeigt. Zahllose Messreihen mit allerlei Schmierstoffen zeigen, dass – je nach Schmierstoff – Abweichungen von über 50 Prozent möglich sind.
Weil die Druckflächen von Gewinde und Unterlegscheiben nur wenige Quadratmillimeter klein sind, ruft das bei hohen Drehmomenten (und viel Druck auf diese Flächen) obendrein „Ruckgleiten“ oder „Stick-Slip“ hervor. Hier lässt sich der Schlüssel plötzlich wie von selbst bewegen, um dann im nächsten Moment bombenfest zu stehen: bei diesem Übergang von Gleit- zu Haftreibung lässt sich gar nichts messen oder genau einstellen.
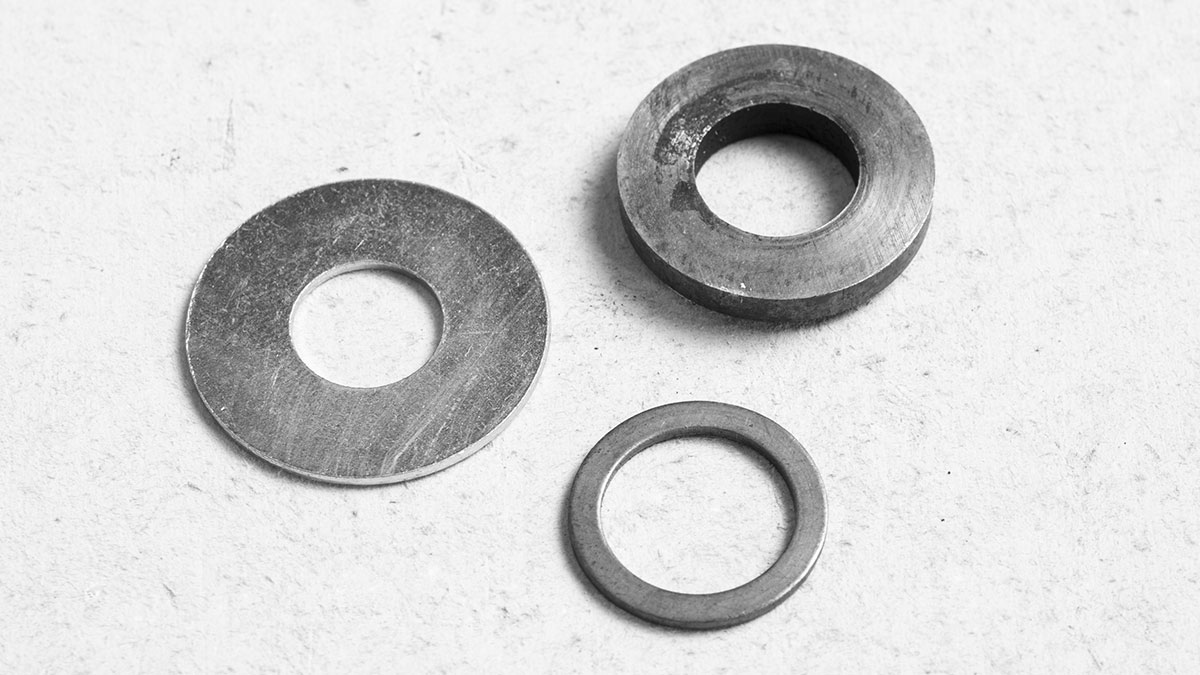
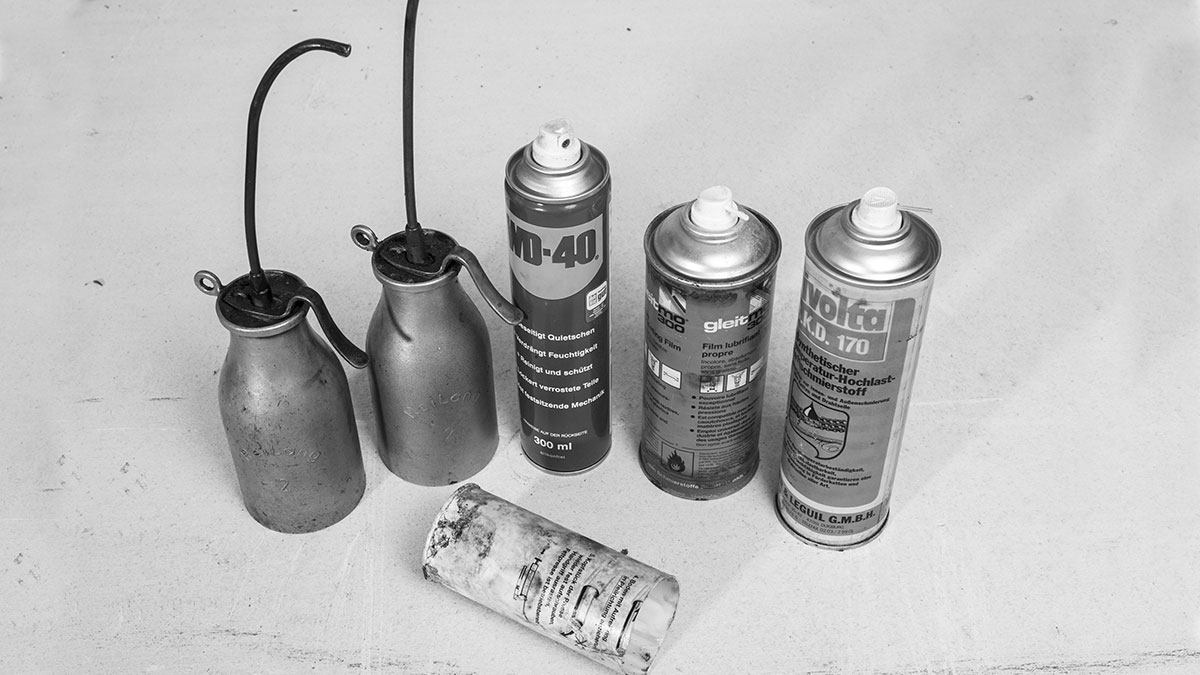
Ruckgleiten = SlipStick
Wer öfter Zylinderköpfe wechselt, kennt diesen Effekt. Besonders deutlich tritt SlipStick bei hohen Druckspannungen auf – und damit besonders im Bereich „kurz vor fertig“, also wenn es auf das genaue Drehmoment ankommen soll.
In unserem Versuch zeigte insbesondere WD40 diesen Effekt. Damit ist das Amisprüh deutlich weniger druckstabil als das gute alte GleitMo, das die Reibung ebenfalls erheblich herabsetzt. Hier tritt jedoch kein Ruckgleiten auf; das Zeug verringert die Reibung fast linear.
Beim Anziehen von Schraubenverbindungen kommt es also (mindestens) auf folgend Punkte an:
– Das Schraubenmaterial (Schwarzer Stahl, Edelstahl, Phosphatiert)
– Ist die Schraube schonmal „gelaufen“? Bei benutzten Schrauben sind die Gewinde aufeinander eingelaufen und haben weniger Reibung
– Auf welcher Fläche stützt sich der Schraubenkopf ab? Je mehr Reibung zwischen Kopf, Scheibe und Werkstück, desto mehr Drehmoment ist nötig
– Sind Reibstellen trocken oder geschmiert? Und wenn ja, womit? Insbesondere MOs-Schmiere setzt die Reibung enorm herab
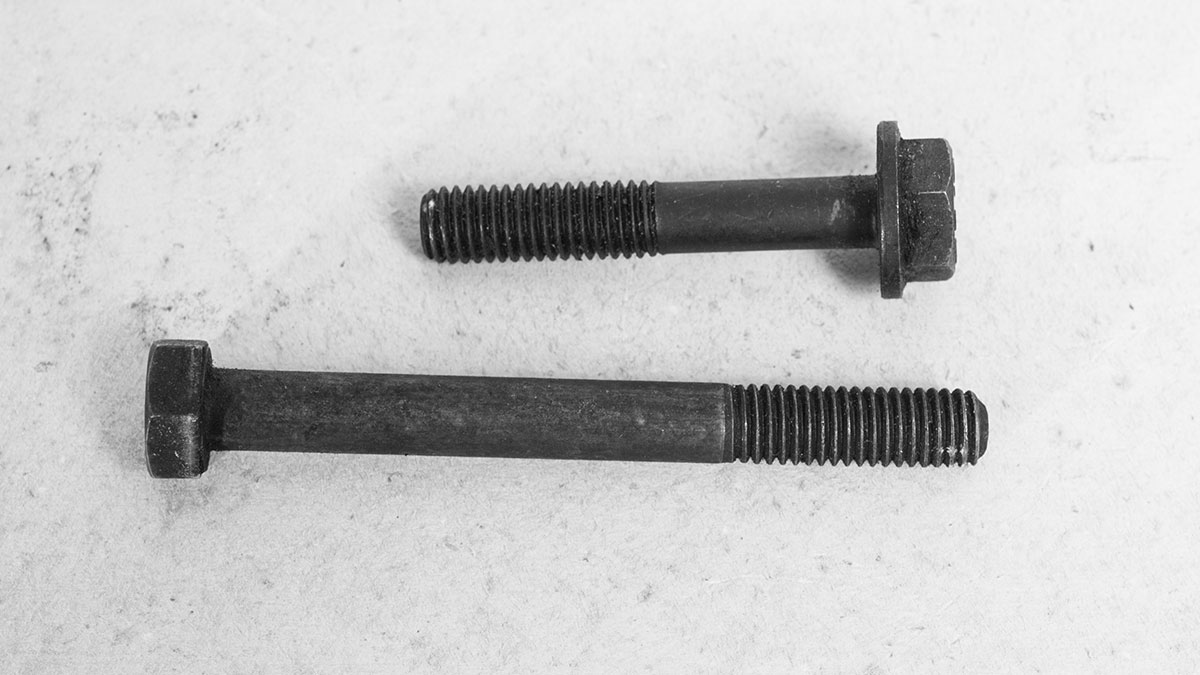
Letzte Aktualisierung am 2024-04-05 / Affiliate Links / Bilder von der Amazon Product Advertising API
Schrauben wie anziehen?
Der hässliche Einfluss von Schmiere auf Reibung und Drehmoment wird auch an Maschinenbau-Hochschulen gelehrt und sollte dem Konstrukteur präsent sein, wenn er eine Schraubenverbindung dimensioniert. Wie kann der arme Mann aber sicherstellen, dass zwischen zwei Bauteilen diese oder jene Klemmkraft herrscht? Schließlich ist er nur auf die Klemmkraft scharf – die Newtonmeter in der Schraube sind ihm ja ziemlich wurscht.
Genau: Er zäumt die Hütte von hinten auf. Dazu hat er in seiner Rechnung zwei konstante Größen: die Klemmkraft und die Steigung des Gewindes. Mit ein bisschen Rechnen kommt er dann auf einen bestimmtes Drehmoment, z.B. „150 Nm am Pumpengehäuse“ – fertig.
Der Mann WEISS, dass ein gut geöltes Gewinde die Klemmkraft des Gehäuses deutlich erhöht. Möglicherweise steigt der Druck auf die Dichtung um 50% gegenüber dem trockenen Gewinde und gleichzeitig geht die Zugspannung in der Schraube ebenfalls hoch. Diese Tatsache ist ihm nicht wirklich egal – allerdings kann er nicht viel dagegen tun.
Maßnahme Nummer eins sind Anzugsmomente und Hinweise, die er in Datenblätter oder Serviceanleitungen schreiben lässt: Schraube x mit 150 Nm anziehen – TROCKEN. Dummerweise hält sich nur selten jemand dadran. Und wer zum Teufel bekommt eine Bohrung im Motorblock wirklich knochentrocken? Zumindest bei Radbolzen mit Kugelsitz sollte man sich hier jedoch dran halten. Die Auflagefläche ist besonders groß und nicht wirklich schwer sauberzumachen.
Nummer zwei ist die kontrollierte Reduktion der Reibung – er lässt den Ersatzteilheini eine Tube Super-Gleit mit in den Reparatursatz legen. Wenn der Mechaniker das Gewinde und die Unterlegscheiben mit diesem Zeug einschmiert, setzt er die Reibung gleichmäßig und kontrolliert herab. Das ist in jedem Fall deutlich besser als die Hoffnung auf ein trockenes Gewinde.
Möglichkeit Nummer drei ist ein Kompromiss und spart das Fitzelchen Super-Gleit in der Dichtungs-Schachtel. Wie wir oben gesehen haben, tritt das extrem verfälschende Ruckgleiten besonders auf dem letzten Meter auf. Also dann, wenn das Drehmoment an der M14 Zylinderkopfschraube von 150 auf 220 Nm hochgehen soll. Der Hinweis „Alle Schrauben gleichmäßig bis zum erforderlichen Drehmoment anziehen“ ist bei eingeölten Schrauben eher witzlos – es stuckert und ruckert im Drehmomentschlüssel: An kontrolliertes Anziehen ist hier nicht mehr zu denken.
Deswegen teilt der Konstrukteur den Prozess auf. Er lässt bis 150 Newtonmeter per Drehmoment anziehen und schaltet dann auf drehwinkelgesteuertes Anziehen um. Wie im Theoriekapitel beschrieben, geht es ihm ja um die Klemmkraft, nicht um das Drehmoment. Und wenn er Zylinderkopfschrauben anschließend um 3 x 90° nachziehen lässt, schaltet er die Reibung und das Ruckgleiten quasi aus. 3 x 90° sind immer dasselbe – egal, ob das Gewinde ölig, fettig, trocken oder mit Knoblauch mariniert ist.
In den kommenden Folgen deswegen alles zu den Gerätschaften für das saubere Drehmoment. Bis dahin ölen wir nochmal unsere Kehle mit etwas Mümmelmeister durch. Prost allerseits!
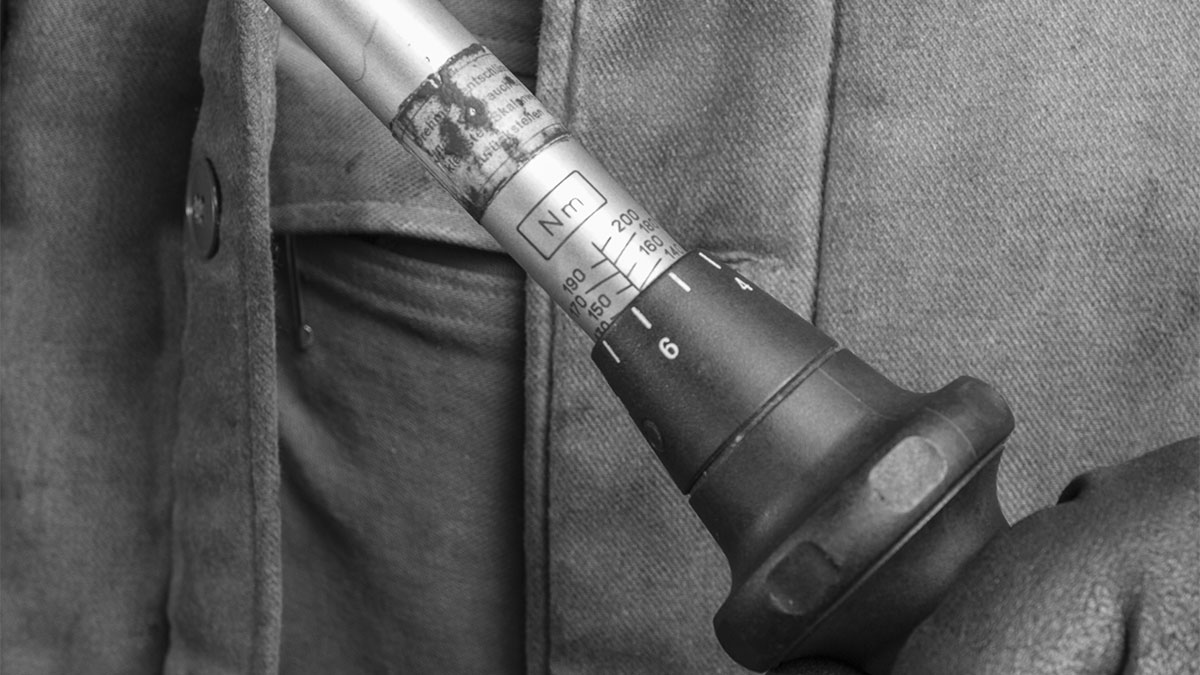