Bügelmessschraube – Aufbau
Eine Bügelmessschraube ist vom Aufbau her simpel und einfach. Sie besteht im Prinzip aus einem stabilen Bügel, an dessen einem Ende ein Amboss mit Messfläche eins sitzt und einer Feingewindemutter. In dieser Feingewindemutter steckt eine Spindel, an deren Ende sich Messfläche zwei findet.
Dreht man die Messspindel rein und raus, so ist der Abstand der Messflächen zueinander genau durch die Steigung der Spindel definiert. Damit man das Messergebnis ablesen kann, ist als festes Teil am Bügel eine Skala angebracht, auf der beweglichen Spindel befindet sich das Gegenstück, die Skalentrommel.
Diese Skalentrommel ist das, was man dreht, um die Dicke eines Werkstücks zu bestimmen. Weil die Spindel aber nur eine geringe Steigung von in aller Regel 0,5mm hat, lassen sich mit einem beherzten Dreh leicht Kräfte von ein paarhundert Kilo (oder Newton…) aufbringen.
Das kann im Notfall dazu dienen, Haselnüsse unterm Werkstatttannenbaum zu knacken, ruiniert aber das teure Messwerkzeug, das Werkstück und sorgt für Messwerte mit der Aussagekraft eines Aserbaidschanischen Wahlergebnisses. Damit man also immer dieselbe (! – wir erinnern: Wiederholungsmessungen) Kraft zwischen beiden Messflächen hat, ist am Ende der Trommel ein Drehmomentbegrenzer eingebaut. Diese kleine Rutschkupplung sorgt dafür, dass die Messkraft stets gleich bleibt.
Um das Messergebnis des abends den staunenden Nachbarn am Stammtisch zu präsentieren, kann man die Messspindel mit einer kleinen Schraube oder einem Knebel festklemmen. Das hat durchaus seinen Sinn, wenn man seine trüben Augen nicht unausgesetzt auf die Skala richten kann oder, mit leichter Demenz geschlagen, jeden Wert zwischen Werkbank und Drehbank schon wieder vergessen hat.
Dass die Klemmung normalerweise los ist, weil sie sonst die Spindel verschleißt, versteht sich von selbst. Geht die Klemmung bei einer gebrauchten Schraube nicht, so lässt das u.U. schon auf den Verschleiß des guten Stückes schließen.

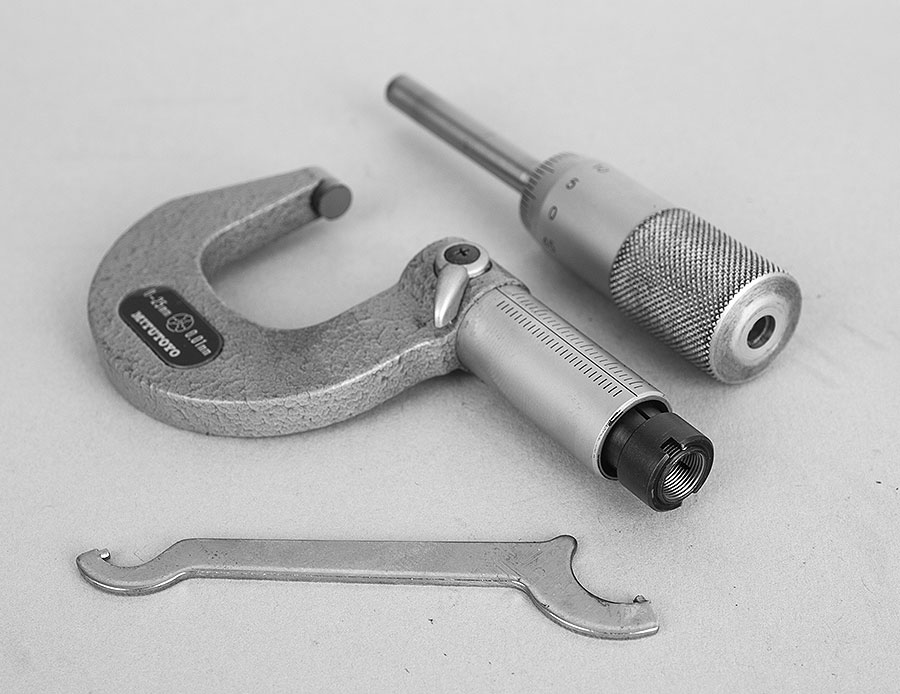
Messschraube zerlegen
Ob der Messprügel taugbare Werte liefert, lässt sich leicht überprüfen – wenn man denn ein passendes Endmaß hat. Das kann aus dem hypergenauen Endmaßkasten stammen oder schlicht zwecks Kalibrierung der Schraube mit in der Schatulle liegen.
Ist die Schraube dejustiert, d.h. zeigt sie nicht das an, was auf diesem Endmaß steht, so muss man das Messgerät zerlegen. Neben dem Endmaß zum Justieren des teuren Messwerkzeugs findet sich dazu in der Schatulle hoffentlich auch ein kleiner Hakenschlüssel, mit dem man in aller Regel die Drehmomentratsche am hinteren Teil der Schraube herunterbekommt. Ist dieses kompakte Teil ab, lässt sich die Messspindel mit Skalentrommel ganz aus dem Messbügel herausdrehen.
Liegen die Einzelteile weich und in samtenen Tüchern gebettet, so wird man der Einstellmutter im Bügel gewahr – dieses Ding ist verdrehbar darin eingelassen und ermöglicht eine hundertprozentige Justage der Bügelmessschraube.
Weil von dieser Arbeit aber das Wohl und Wehe der Kurbelwelle des frisch zerlegten U-Boot-Diesels abhängt, macht man das am besten nicht der zugigen Toschihalle, sondern mit viel Ruhe im Herzen und sauberen Fingern abends am Schreibtisch.
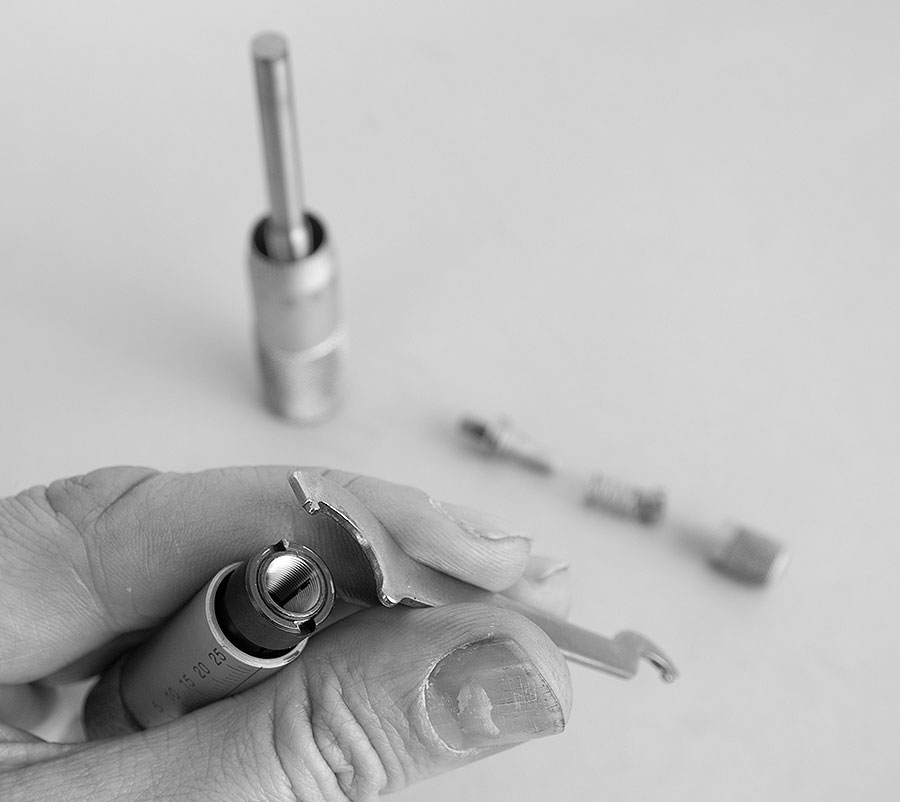
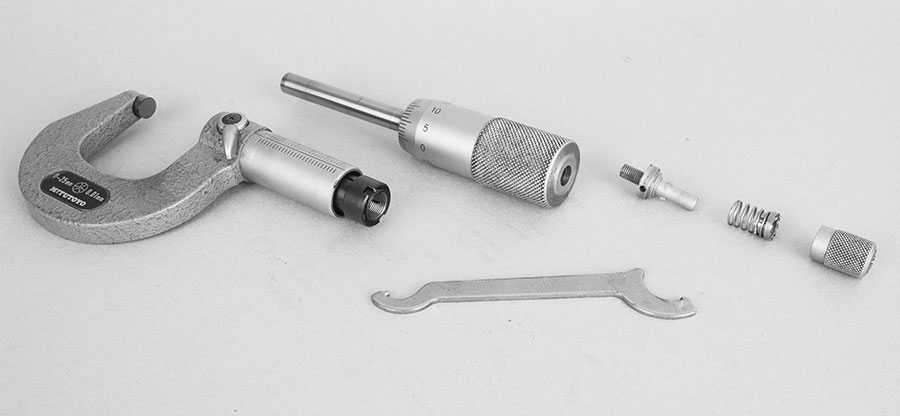
Kalibrierlabor Küchentisch
Wer in digitalen Zeiten nur noch den Desktop hat, kann die Arbeit auch Küchentisch erledigen: Neben absoluter Sauberkeit benötigt man dazu vor allem jenes Endmaß, dass einen festen und absolut genauen Wert verkörpert und auf den hin man die Schraube einjustiert. Dazwischen steht ein wiederholtes Auseinander- und Zusammenbauen, bis das Ding genau das anzeigt, was es soll.
Die Spindel wird mit leichtem, teuren Maschinenöl oder Ballistol geölt – nie mit Fett oder harzigem Krimskrams. Dass die Messflächen beim Justieren absolut sauber und frei von Macken sein sollten, versteht sich von selbst – ansonsten baut man sich einen permanenten Fehler in die Messungen, der selbst kluge Köpfe an den Rand des Wahnsinns bringt.
Stuckert die Messspindel während einer Umdrehung, so kann man fast davon ausgehen, dass die Schraube mal Bodenkontakt hatte. Lässt sich das mit einer gründlichen Reinigung (mit sauberen Tüchern, homöopathischen Dosen Nitroverdünner und leichtem Öl) nicht beseitigen, ist vermutlich die Spindel krumm – das Gerät taugt dann bestenfalls noch als Schätz-Eisen.
Das gilt auch für diejenige Bügelmessschraube, deren Spindel in einem Bereich sehr flutschi läuft und an einer anderen Stelle fast klemmt. Dieses Teil hat seine besten Tage auch hinter sich und wurde vermutlich an einem einzigen Maß abgearbeitet.
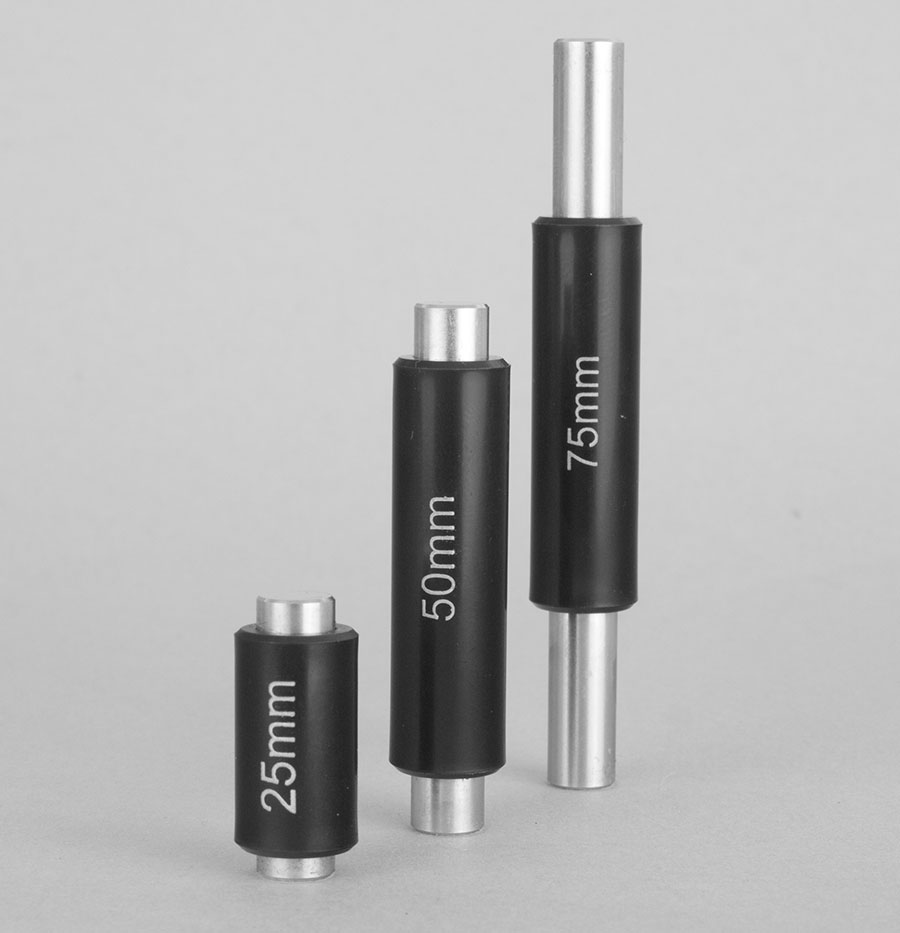
Drehmoment und Sauberkeit
Bevor man jedoch mit sauberen Fingernägeln, dezenter Musik und wohltemperierten Werkstücken ans Messen geht, steht noch die Überprüfung der Bügelmessschraube an: Zeigt das Gerät auch wirklich das an, was es soll? Hier hilft vor allem portentiefe Reinheit der Messflächen.
Bei einer Schraube 0-25mm ist das einfach: Den Hosenlatz der Arbeitshose ins Visier nehmen, die Schraube sachte andrehen und ein wenig hin- und herziehen. Jetzt sollten Spindel und Amboss sauber sein. Diese Prozedur bringt manchmal ein erstaunliches Hundertstel – und um das geht es ja. Bei größeren Schrauben und Messbereichen putzt man mit weichen Lappen so lange, bis man sich in der Fläche spiegeln kann.
Alles Messen mit der Bügelmessschraube wird einzig und allein mit der Ratsche, der Drehmomentbegrenzung vorgenommen. Direkt an der Skalentrommel dreht man nur, um den toten Weg bis zum Messpunkt zu überwinden. Geht man also die letzten Zehntel mit der Ratsche durch, dreht man langsam und mit Gefühl. Dieses langsam ist auch wichtig, weil man sonst mit viel Schmackes die Messkraft auch verfälscht und Nüsse knacken kann.
Ist man nicht sicher, dreht man noch mal los und versucht es sinnig und langsam zum zweiten Mal.
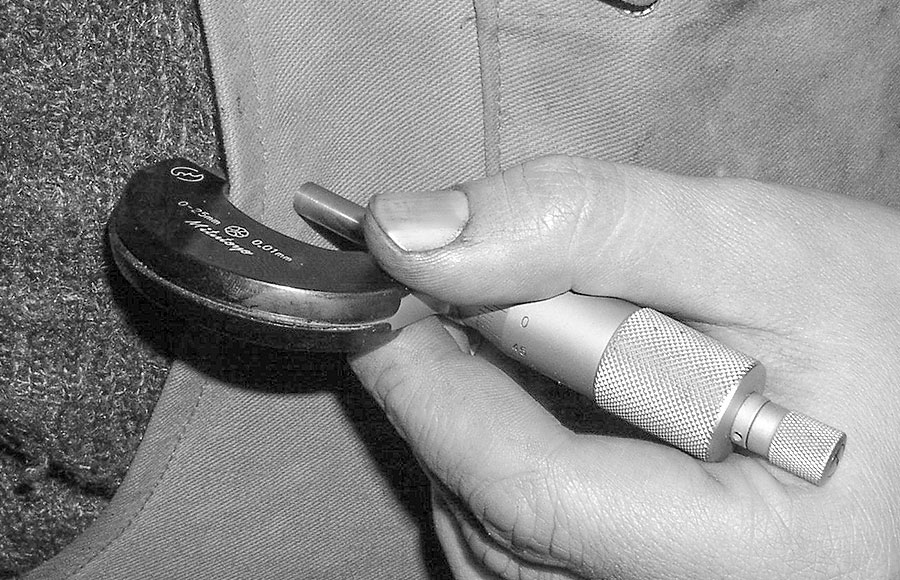
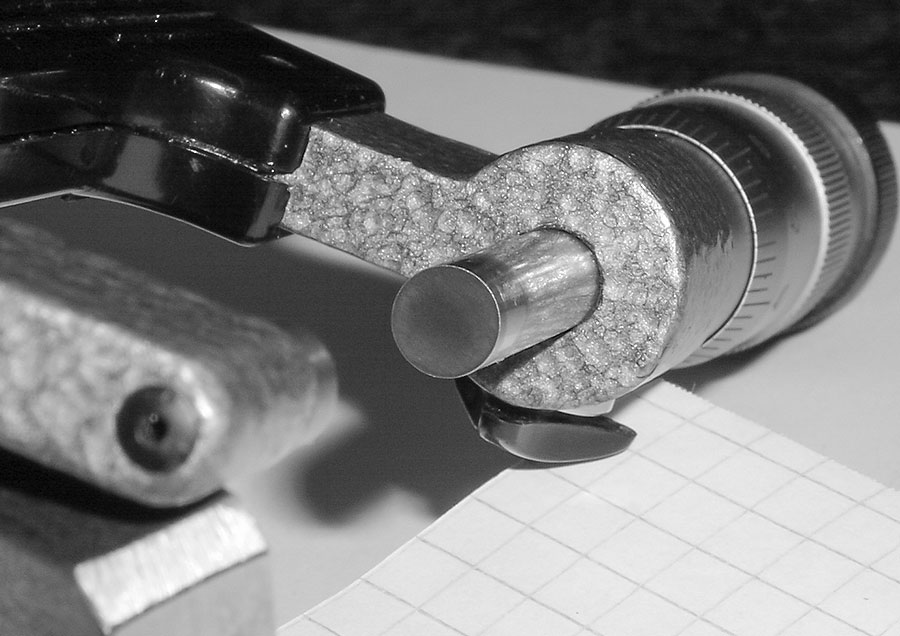
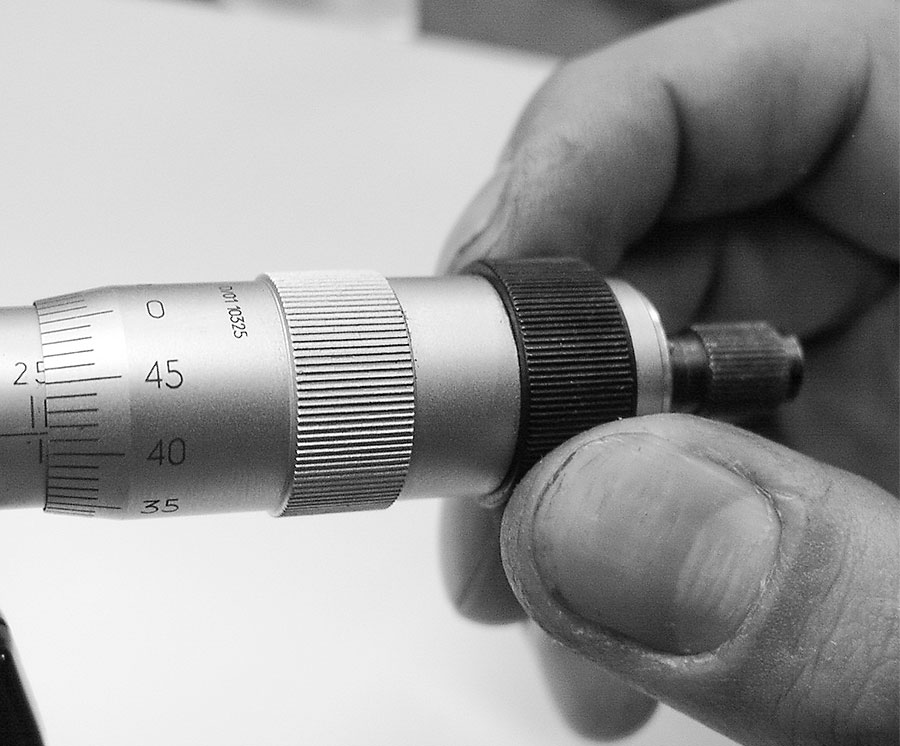
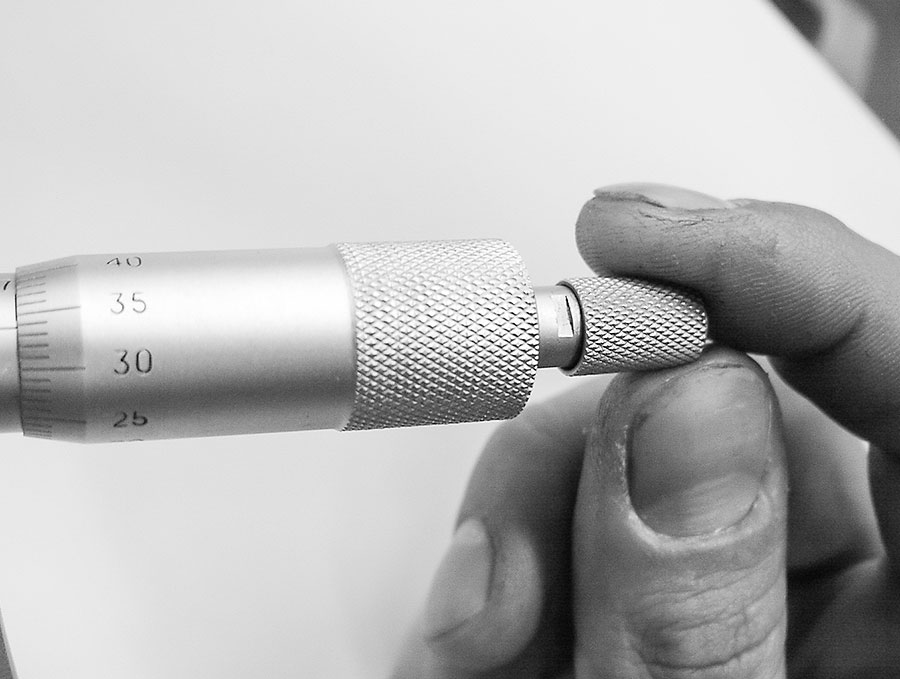
Auf Null?
Vor aller Messerei steht aber die Überprüfung des teueren Messzeugs: Bei der Schraube mit 0 – 25mm die Spindel ganz zusammendrehen, bei allen größeren das Endmaß zwischenhalten. Spindel mit der Ratsche anziehen und Wert ablesen: Steht das Ding genau auf Null (oder 25,00 oder 50,00 etc.)? Wenn ja: Prima. Wenn nein, justieren.
Darüber hinaus sollten sich alle Fehler oder Missweisungen wiederholen lassen. Wenn man also beim Zusammendrehen einer 0 – 25mm-Schraube immer wieder 0,01 angezeigt bekommt, kann man fast davon ausgehen, dass echte 20,00mm von diesem Gerät als 20,01 dargestellt werden.
Mit Papier, Bleistift und Gehirnschmalz lässt sich also auch aus einem alten Delter noch was Vernünftiges herausmessen. Allerdings sollte man sich so ein Gerät bei nächster Gelegenheit zur Brust nehmen oder entsprechend markieren.
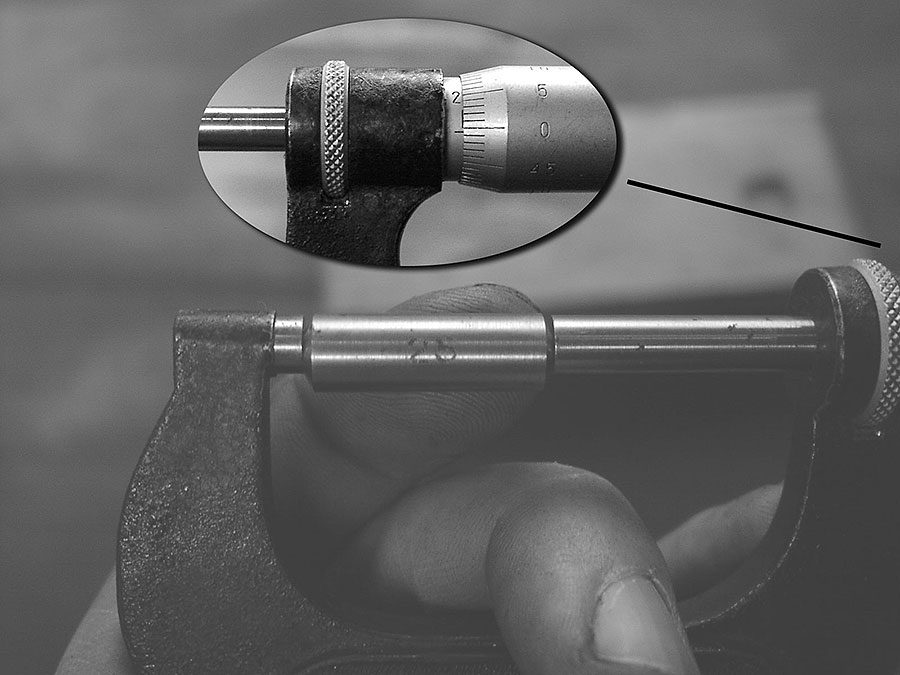
Doppelter Dreh
Die Spindeln der meisten Bügelmessschrauben haben eine Steigung von 0,5 mm. Das bedeutet, dass die Messspindel bei einer Umdrehung 0,5 mm raus- oder reinfährt. Umgekehrt heißt das für den fragenden Benutzer, dass ein ganzer satter rein-raus-Millimeter ZWEI Umdrehungen der Skalentrommel zur Folge hat. Es gibt auch andere Teilungen, gebräuchlich ist aber diese.
Weil also zwei Umdrehungen auf der Skala dargestellt werden wollen, gibt es eine Skala für ganze und eine Skala für halbe Millimeter. Entsprechend geht die Einteilung der Trommel auch nur von 0 – 50. Diese 0 – 50 sind Hundertstel. Die anderen 50 – 100 Hundertstel verstecken sich in der zweiten Skala. Will man deswegen xx,74 messen, dirigiert man seine Augen auf die zweite Skala (oder Hälfte) und hat xx,24 eingestellt. Die fehlenden 50 Hundertstel addiert man im Kopf.
Hier im Bild sind ein paar Messwerte als Beispielwerte eingestellt. Zum Üben einfach irgendwas ins Korn nehmen und rumprobieren. Über das waschechte Hundertstel, dass jede Messschraube bringen kann und muss, sind die Tausendstel, die sich hinter den Hundertstel verbergen, auch zu erahnen. Hängt der Zustand einer Passung an so ein paar Tausendsteln, kann man die bei wirklich einwandfreien Bedingungen durchaus zwischen den Teilstrichen auf der Trommel finden. Das erfordert aber 20°Celsius, eine gute Messschraube, porentiefe Sauberkeit und mehrere Messungen,
um ganz sicher zu gehen.
Hat man viel Kleinkram zu messen, lohnt es sich zu üben und die Bügelmessschraube mit einer Hand zu bedienen. Das hält den Rücken grade und erleichtert die Arbeit ungemein. Ist man schließlich mit allem Messen durch, kommt das Kleinod sofort wieder in sein Häuschen und in die hinterste Schublade, damit niemand da Hammer, Schlüssel oder Kurbelwelle draufstellt. Oder blind wie ein Maulwurf mit seinem Lanz drüberweggurkt.
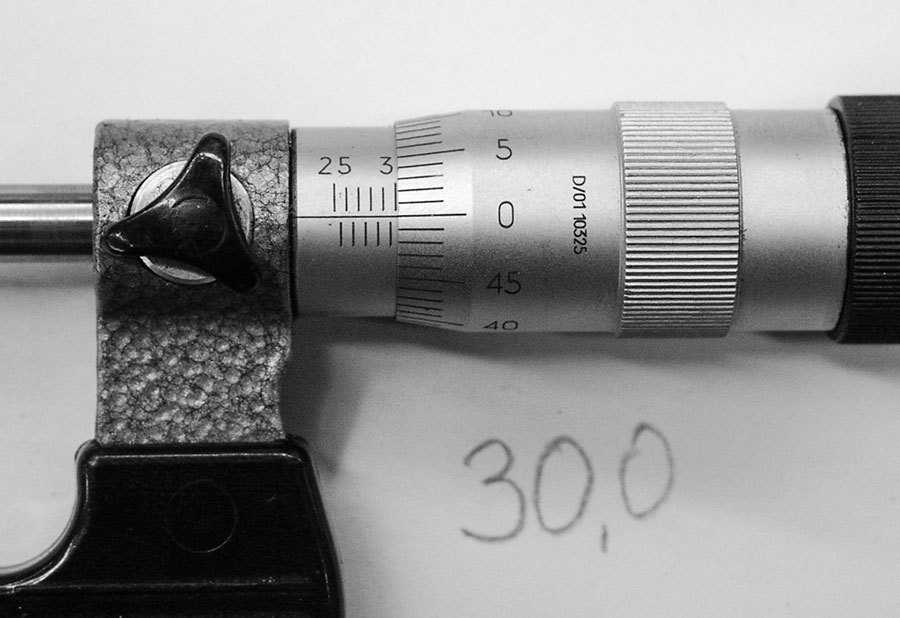
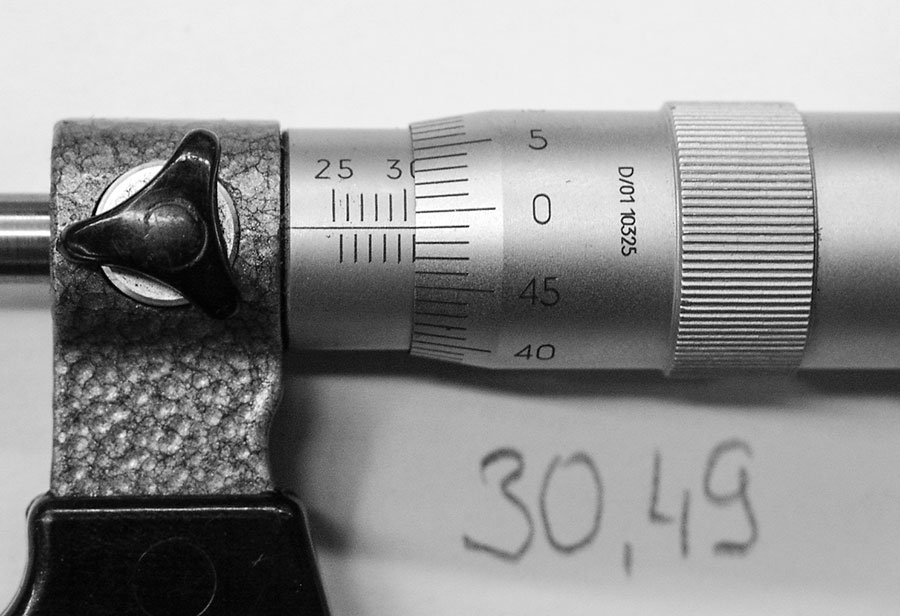
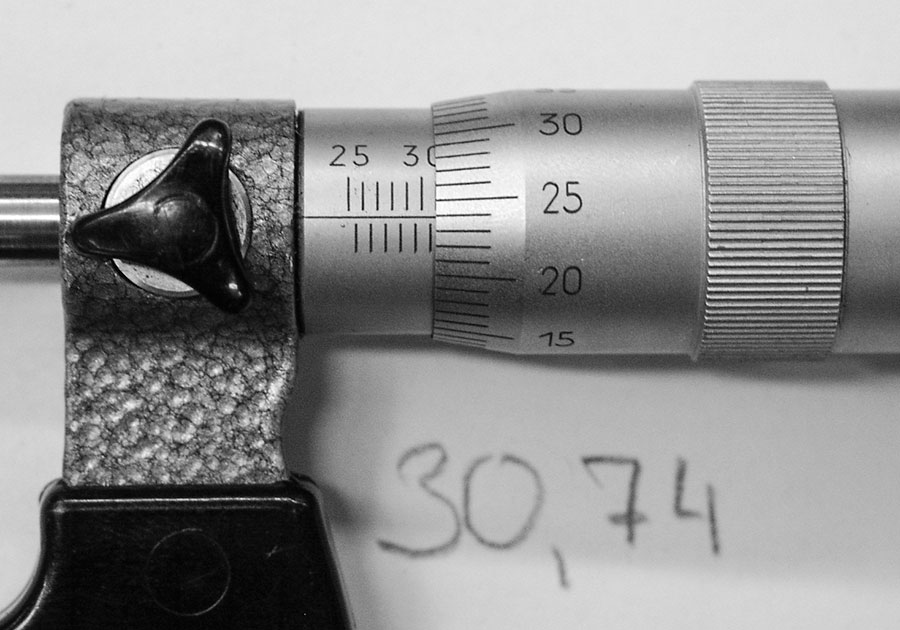
Letzte Aktualisierung am 2024-04-05 / Affiliate Links / Bilder von der Amazon Product Advertising API
Gut gewärmt
Holt man das teure Messgerät aus seinem Holzkistchen und schleicht sabbernd zur Kurbelwelle, kann ein Blick aufs Thermometer nicht schaden: Begibt man sich nämlich in das Zauberreich der Mikrometer, so tun hier ein paar Celsius-Grade mehr oder weniger schon ganz erstaunliche Dinge.
Alles (von Wasser am Anomaliepunkt mal abgesehen) wird kleiner, wenn man es abkühlt und größer, wenn man es warmmacht. Diese Wärmeausdehnung ist bei jedem Werkstoff verschieden und sorgt dafür, dass z.B. Gleisbauarbeiten bei der Bundesbahn im Sommer nur Nachts passieren, weil tagsüber zuviel Musik in den sonnenbeschienen Gleisen ist.
Im Reich der kleinen Dinge ist diese Ausdehnung aber auch nicht zu verachten: Ein Drehteil von vielleicht 20 mm Durchmesser (ein Wellenzapfen oder Bolzen) macht bei größeren Temperaturdifferenzen auch schon eine interessante Metamorphose durch. So hat zum Beispiel Chromnickelstahl laut Tabellenbuch einen Wärmeausdehnungskoeffizienten von 0,000016. Das heißt, dass sich eine Stange aus dem Zeug bei einem Grad wärmer oder kälter um den Faktor 0,000016 ausdehnt oder zusammenzieht.
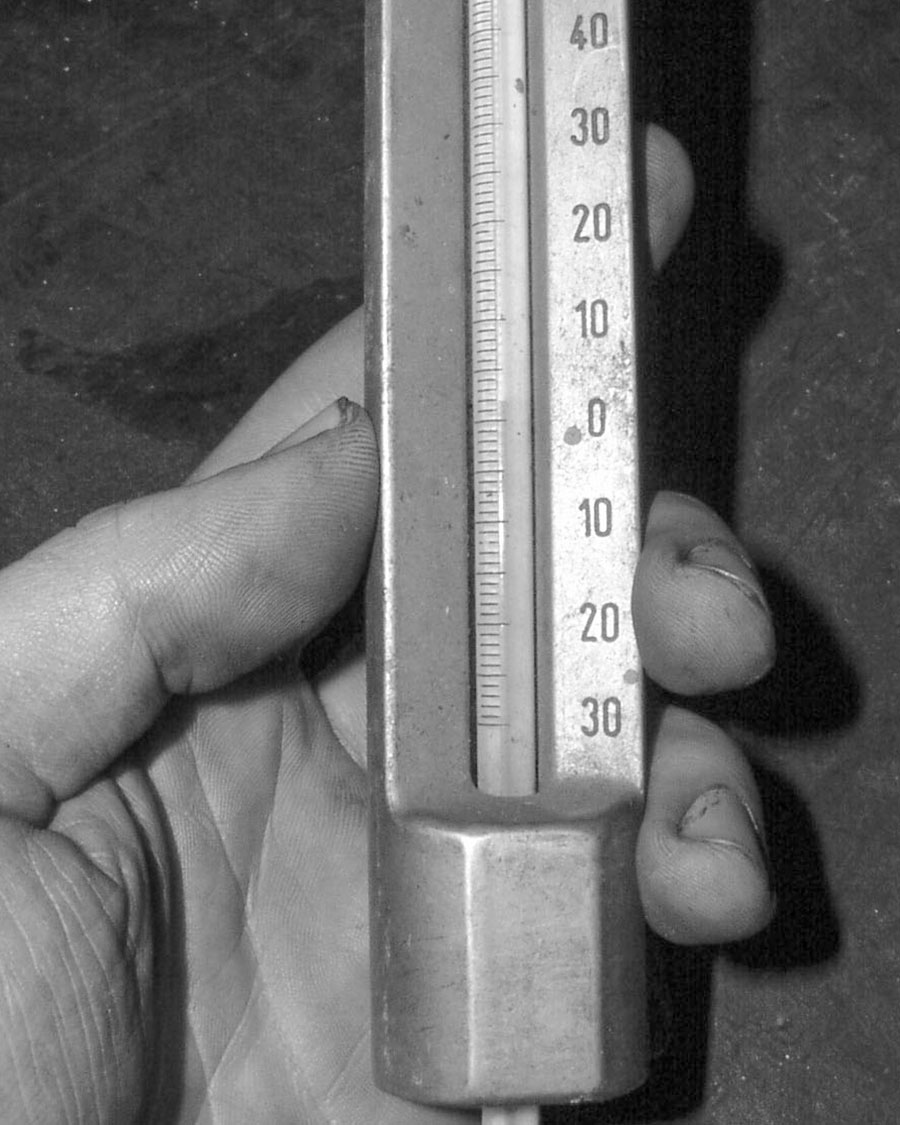
Passung passend?
Auf dem Bildschirm machen die 0,000016 nicht viel her, hauen aber in der Realität gewaltig ins Kontor. Die Bezugstemperatur, die für alle Teile auf der großen weiten Welt gilt, sind 20° Celsius. Alle Längenmaße von Nordpol bis Neapel beziehen sich deswegen auf 20° Celsius. Wenn man also den Wellenstumpf des Schneemobils am Nordpol und Minus 30° mit der Bügelmessschraube traktiert, ist das Ding kleiner, als wenn es bei Mama Mancini in Neapel zwischen Stilett und Pasta-Schüssel im Sommer auf der Fensterbank lag.
Nimmt man im ersten Fall einen Temperaturunterschied von 50° gegenüber der Bezugstemperatur von 20° Grad an, so ist die Rechnung folgende: 50 (Temperaturdifferenz) * 20 (Durchmesser Welle) * 0,000016 = 0,016. Das sind immerhin solide 1,6 Hundertstel. Bei einer Übergangspassung h7 der 20er Welle hat man ein Grenzabmaß von 20,000 bis 19,979 mm. Da können 1,6 Hundertstel ganz schön viel sein und eine noch gute Welle zum Ausschuss, weil Untermaß, machen. Bei zu heißen Werkstücken ist es im Prinzip genau dasselbe.
Wenn man also bei winterlichen Temperaturen in der Werkstatt schraubt und misst, sollte man die Teile entweder mit in die warme Bude nehmen und dort auftauen und messen oder die Ausdehnung grob mit im Kopf haben, wenn es nicht so drauf ankommt.
Die Bügelmessschraube selbst betrifft diese Wärmeausdehnung natürlich auch – das Ding geht ebenfalls nach dem Mond, wenn man es auf dem spuckheißen Spindelkasten der Drehbank liegen hat und dann ein eiskaltes Werkstück angeht. Heiße Schraube und heißes Werkstück sind schon gar nicht schlecht, aber wegen verschiedener Ausdehnungskoeffizienten und Temperaturen schlicht unkalkulierbar. Beim Messen also die Schraube immer an der lustigen Griffplatte anpacken, die eine Wärmeleitung in den Bügel verhindern soll.
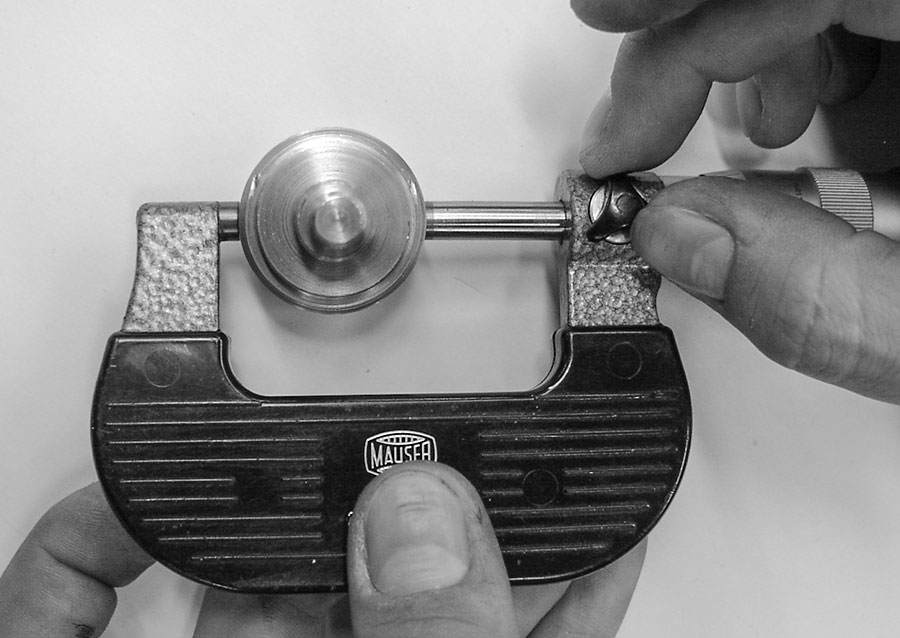