Säulenbohrmaschine – überall
Die Säulenbohrmaschine ist neben Werkbank, Schraubstock und Feile das elementare Hilfsmittel jeder Schlosserei – weltweit. Betritt man das dämmrige Halbdunkel einer Jeep-Reparatur im pakistanischen Hochland, wird neben Schmiedefeuer, Schweißtrafo und einer Chapatti-Pfanne auch irgendwo eine Säulenbohrmaschine herumstehen.
Hatten wir in der vergangenen Folge den Bohrständer als Mittelchen, um mit einer gemeinen Handbohrmaschine eine Tisch- oder Säulenbohrmaschine zu emulieren, so stößt dieses Bohren im Bohrständer irgendwann auf eine Grenze – und diese Grenze ist schlicht der Durchmesser des Werkzeugs. Bohrer mit über 10mm Durchmesser haben nämlich keinen gewohnten Zylinderschaft mehr, sondern werden über so genannte Morsekegel in der Bohrspindel gehalten.
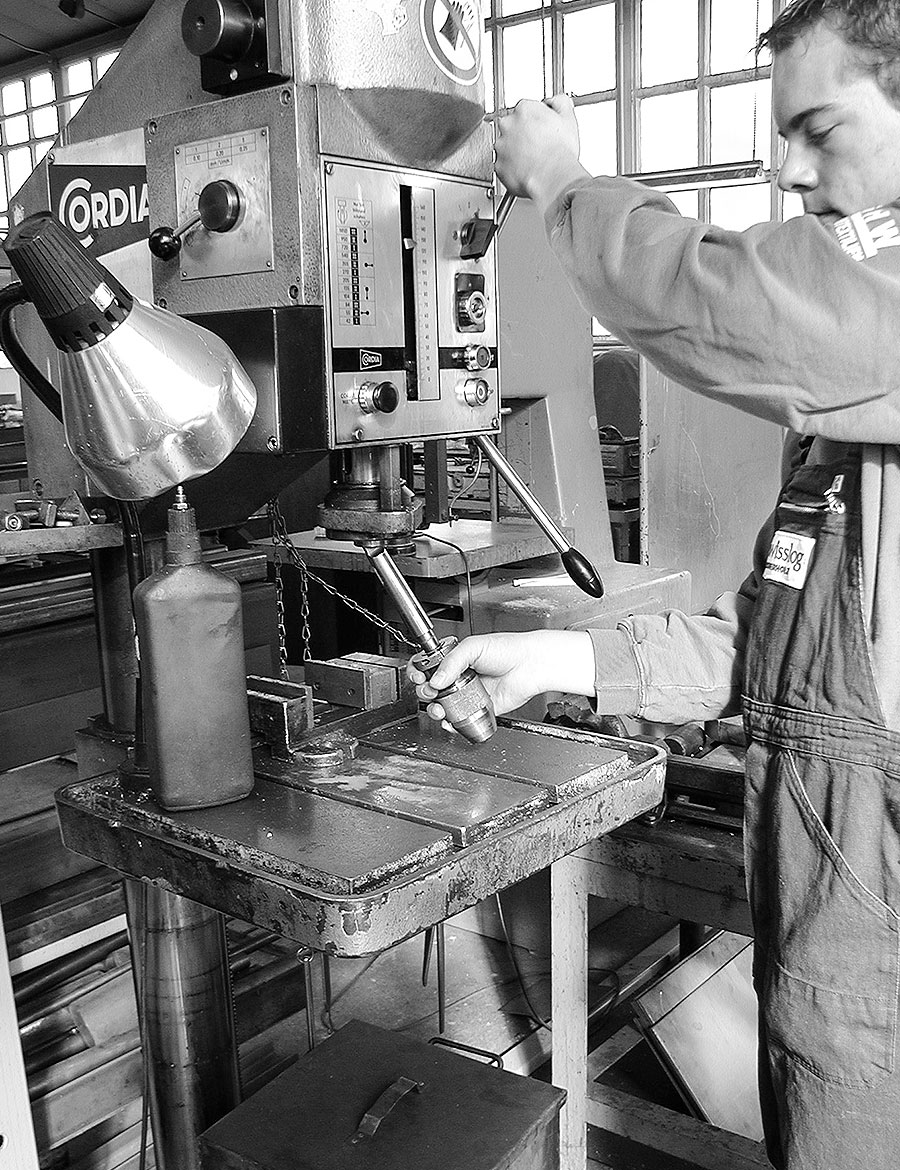

Morsekegel
Diese Morsekegel tragen die sinnfällige Abkürzung „MK“ und sind schlanke Kegel, die die Bohrkraft ausschließlich über die Fläche der Kegel übertragen. Je nach Durchmesser des Werkzeugs existieren auch verschiedene Größen von Morsekegeln. Kleinste Nummer, haha, ist natürlich MK0. Spiralbohrer mit einem Durchmesser bis 14mm haben eine Aufnahme mit MK1, bis 23mm MK2 und darüber MK3 und so weiter.
Bohrer, Reibahlen oder Senker mit größerem Genummer kommen im üblichen Gebrauch schlicht nicht vor und benötigen Bohrwerke oder Drehbänke mit den Abmessungen einer Doppelgarage. Damit aber in eine große Maschine auch ein kleines Werkzeug eingebaut werden kann, gibt es Adapter.
Diese Adapter heißen „Reduzierhülsen“ und machen aus MK3 das kleinere MK2 oder MK1. Wie bei LEGO lassen sich Reduzierhülsen, Spannfutter und Bohrwerkzeuge auch munter miteinander kombinieren. Und gleichzeitig existieren auch Maschinenfutter, die nicht für die Handbohrmaschine gedacht sind, sondern mit Morsekegel ausgerüstet in eine Säulenbohrmaschine eingesetzt werden.
Faszinosum der Morsekegel-Aufnahme ist, dass die Werkzeuge einzig über die Reibung oder Haftung zwischen Kegel und Aufnahme halten. Diese Teile sind so verflucht sauber gepasst, dass damit gewaltige Kräfte übertragen werden können. Um das LEGO-Stecksystem zusammenzufügen, müssen die Flächen von Werkzeug und Spindel von Dreck befreit und mackenfrei sein. Steckt man jetzt einen Spiralbohrer MK1 in eine Reduzierhülse MK2-MK1, so genügt ein simpler, freundlicher Stupser, damit der Kram brutalen Drehkräften standhält.
Setzt man diese Kombination in die Bohrmaschine ein, so genügt ebenfalls ein kleiner Stupser, um Bohrer und Maschine bombenfest zu verbinden. Um alles wieder auseinander zu bekommen, ist auf jedem Morsekegel ein „Austreiblappen“ angebracht. Das Ding ist mitnichten am Bohrer, um ihn mitzunehmen, sondern einzig, um die Reibverbindung des Kegels wieder zu lösen.
Die Spindel oder Hülse, in der ein solcher Bohrer steckt, hat als Gegenstück dazu ein Langloch, durch das man einen Keil schieben kann, um den Kegel vom Grund abzudrücken. Dieser Keil oder Austreiber ist natürlich auch in verschiedenen Größen erhältlich und das zum Werkzeugwechsel unentbehrliches Utensil.

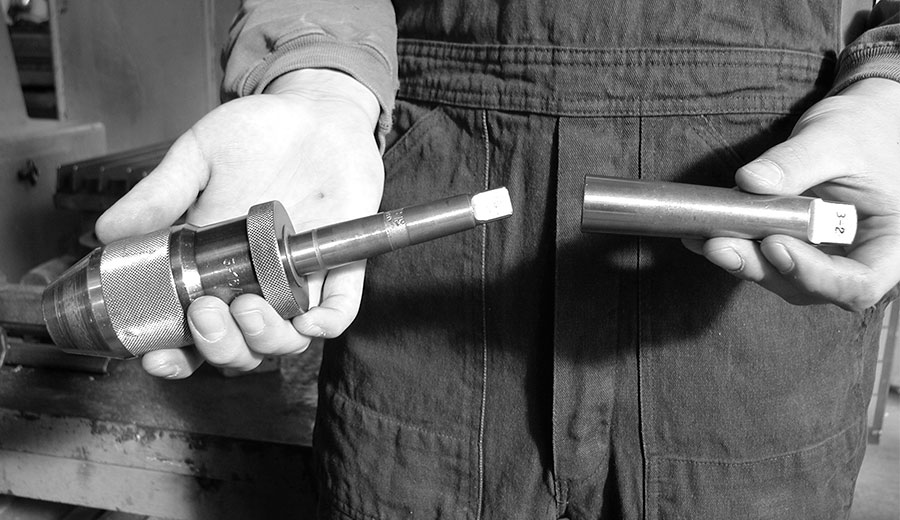
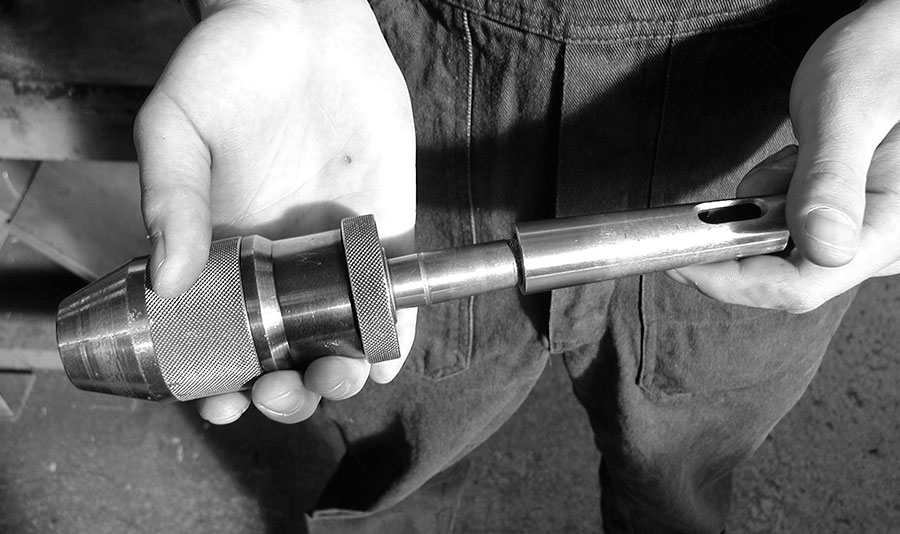
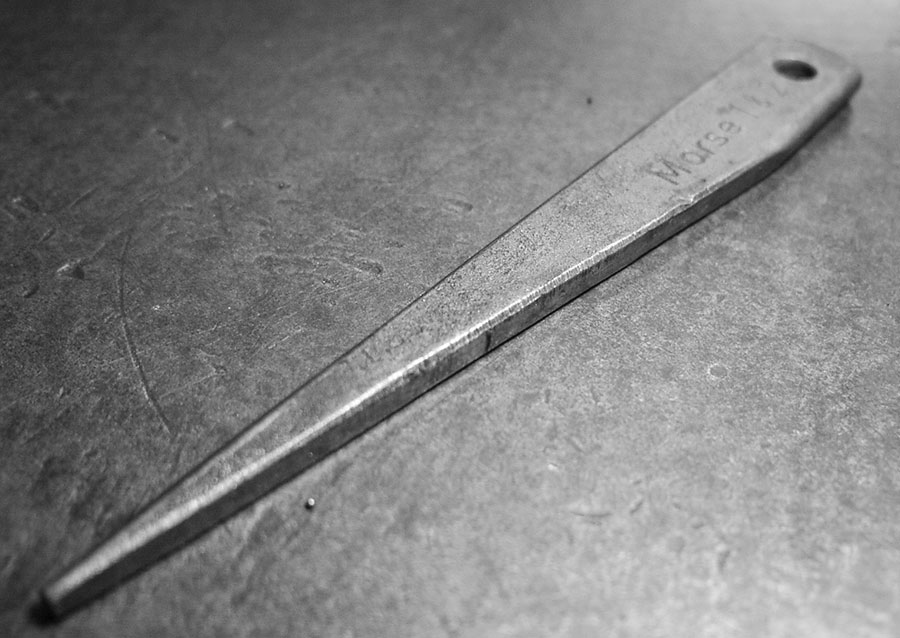


Schwer und freistehend
Eine Säulenbohrmaschine muss vor allem stabil sein. Weil auf den Bohrer je nach Schneidengeometrie (dazu kommen wir noch) hohe Druckkräfte aufgebracht werden müssen, um überhaupt Späne zu produzieren, darf sich die ganze Maschine keinen Muckser verdrehen oder verbiegen. Bei einer mittelschweren Säulenbohrmaschine mit MK2-Spindel können mit dem simplen Handhebel durchaus Druckkräfte von einer Tonne auf den Bohrer gebracht werden, die eine zu weiche Konstruktion wie eine Büroklammer aufbiegen würden.
Die Einheit Tisch-Säule-Spindel ist deshalb bei einer guten Maschine präzise gearbeitet und so großzügig dimensioniert, dass selbst der größte noch in die Spindel passende Bohrer das Trumm nicht in die Knie zwingt. Neben dieser Stabilität stiftenden Wirkung dient die Säule einer Säulenbohrmaschine vor allem zwei Aufgaben. Erste ist, Arbeit im Stehen zu ermöglichen. Die Säule positioniert den Tisch und das Werkstück in einer Arbeitshöhe, die menschenwürdig ist und die Berufsgenossenschaft zufriedenstellt: sie hält das Werkstück von der Erde weg.
Zweiter Zweck der Konstruktion ist, den Tisch auch hoch- und runterfahren zu können. Damit lässt sich die Bohrmaschine sowohl auf kürzere oder längere Bohrer, als auch größere oder kleinere Werkstücke einstellen. Mit einer beweglichen Zahnstange auf Höhe gekurbelt, lässt sich der Tisch nach Lösen der Klemmung auch komplett zur Seite schwenken, um ganz große und hohe Sachen unter die Bohrspindel zu zerren oder von Hand Werkstücke an die Spindel zu halten. Letzteres ist natürlich allen Unfallverhütungsvorschriften zuwider und sollte Notfällen vorbehalten bleiben.
Eine stabile Bohrmaschine ist also präzise gearbeitet, schwer und sollte immer auf dem Werkstattboden festgeschraubt sein. Spannt man nämlich größere und vor allem lange Werkstücke auf den Tisch, so darf die wertvolle Maschine unter keinen Umständen umkippen: das beschädigt nicht nur die teuren Perserbrücken auf dem Fußboden oder verwandelt Schrauberfüße in formschöne Artefakte moderner Kunst, sondern zieht Schäden an der Maschine nach sich. Kauft man eine Maschine gebraucht, sollte deshalb unbedingt untersucht werden, ob das Teil schon mal Bodenkontakt hatte und die Bohrspindel noch rund läuft.
Wichtig auch der Aufstellungsort: in eine Ecke gezwängt, kann man mit der dollsten Bohrmaschine nur kleine Sachen perforieren, weil man nichts durchstecken kann. Optimal steht ein solches Gerät frei im Raum oder wenigstens an einer Wand mit Platz zu beiden Seiten.
Hat die Maschine keinen Fuß und ist direktemang auf der Werkbank festgeschraubt, so heißt man es Tischbohrmaschine. Vom Prinzip her sind sie mit Säulenbohrmaschine baugleich, allerdings spart diese Bauweise Platz und ist nur für „leichtere“ Arbeiten gemacht.
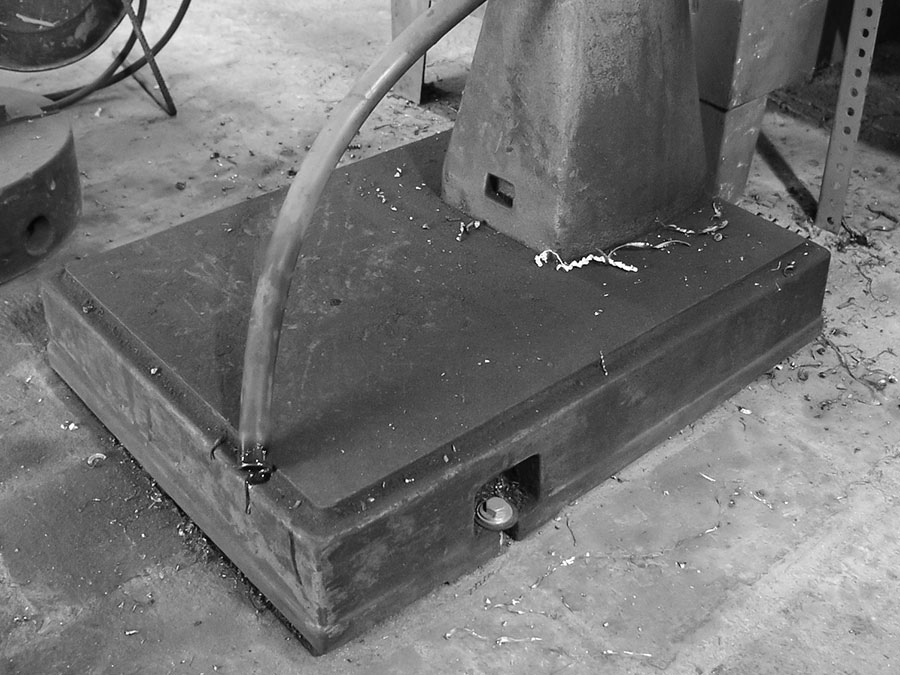
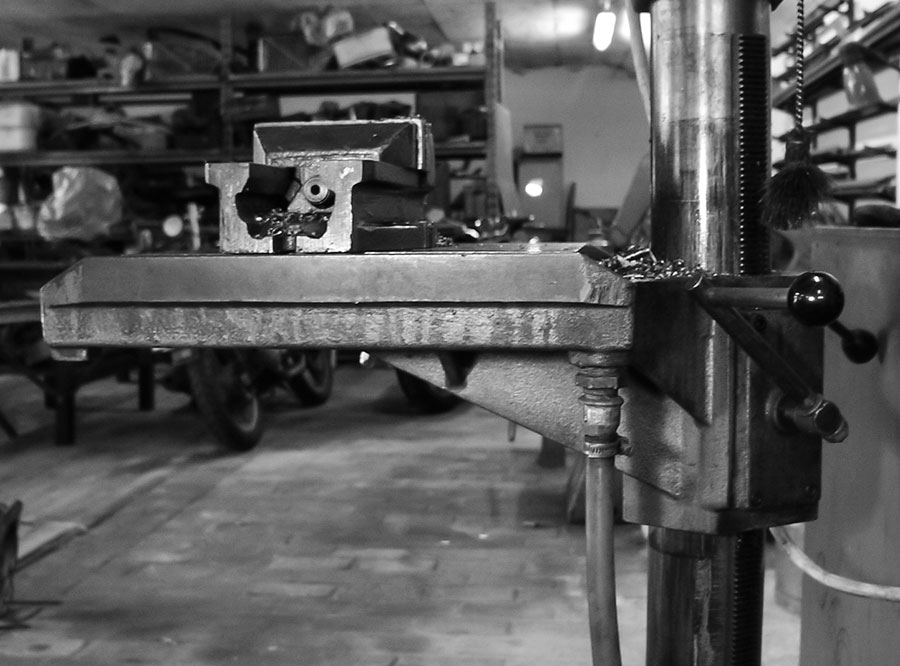
Motor und Getriebe
Ist die Säulenbohrmaschine nun am Boden festgeschraubt und der Tisch fein gedeckt, so finden sich am Kopf der Säulenbohrmaschine allerlei Knöpfe, Hebel, Kästen und Räder. Diese Maschinerie sorgt dafür, dass die Maschine die Spindel in der richtigen Drehzahl dreht und hoch und runter fährt.
Als allererstes braucht man also einen Elektromotor, der den Bohrer dreht. Meist hinten an der Maschine angebracht, konsumieren solche Motoren in aller Regel Drehstrom und leisten ab 500 Watt aufwärts. Typische Drehzahlstufen dieser Asynchronmotoren sind dabei 1000, 1500 oder 3000 Umdrehungen pro Minute. Weil das aber noch kein feinfühliges und angepasstes Bohren möglich macht, hat jede Bohrmaschine auch ein Getriebe.
Mit so einem Getriebe lässt sich die Werkzeugdrehzahl runter- oder raufsetzen und vor allem das Drehmoment an der Spindel potenzieren. Je nach Geldbeutel unterscheiden sich natürlich auch die Bauformen der Getriebe. Hier im Bild ist zuerst die schlichte Variante, bei der die Drehzahl über Riemenscheiben eingestellt wird. Bevor also der Knethaken in den Hefeteig eintaucht, sollte man sich Gedanken über die nötige Drehzahl des Küchengeräts machen (kommt noch genauer) und dann den Riemen umwerfen. Dazu muss der Keilriemen entspannt und auf die richtige Riemenscheibe gelegt werden. In Verbindung mit der richtigen Motordrehzahl ermöglicht die Maschine jetzt kommodes Bohren, Senken oder Reiben.
Richtig langsame Drehzahlen sind allerdings mit dieser Technik nicht hinzukriegen, weil die Riemenscheiben reichlich groß würden und wenigstens in die Maschine hineinpassen müssen. Für ein paarhundert Eulonen mehr stehen Maschinen mit Zahnradgetriebe im Schaufenster. Das ist nicht nur einfacher in der Bedienung, sondern kann auch mehr Kraft übertragen. Mehr Kraft ermöglicht dickere Bohrer und die brauchen niedrigere Drehzahlen. Die Gänge werden mit einem oder mehreren Hebeln eingelegt und ermöglichen schnelleren Gangwechsel, zu dem Spindel und Motor allerdings stillstehen müssen.
Das Modell „Superkomfort“ hat ein stufenloses Getriebe ähnlich der legendären DAF-Variomatic. Mit einem Spezialhebelchen lässt sich hier die Drehzahl bei laufender Maschine verstellen und sorgt quasi für US-amerikanischen Fahrkomfort beim Bohren. Allerdings ist dieses Gimmick teuer und meist nur bei größeren Kalibern zu finden. Weil auch die Leistungselektronik in der modernen Welt günstig geworden ist, lassen sich bei neueren Maschinen Motordrehzahlen stufenlos einstellen, so was ist natürlich besonders fein.
Zusammenfassend lässt sich sagen, dass die Relation Gewicht-Drehzahl ähnlich wie bei Handbohrmaschinen, Drehbänken oder schnellgemachten Vorstadt-Mopeds ist: je leichter, desto höher die Drehzahl.
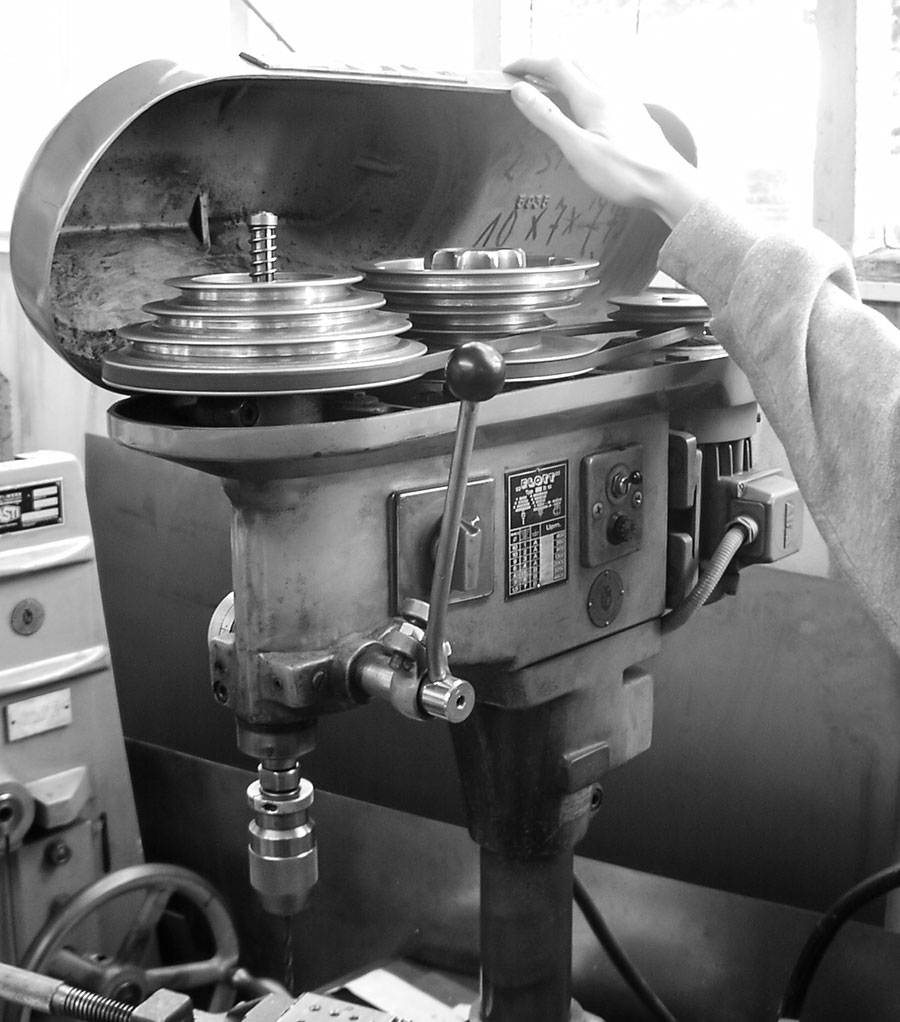


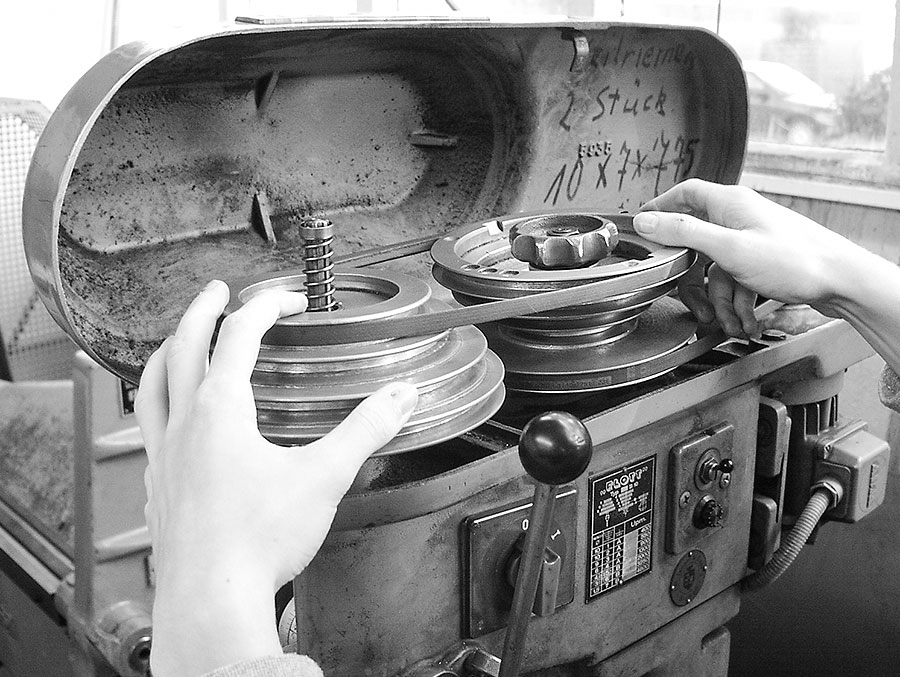


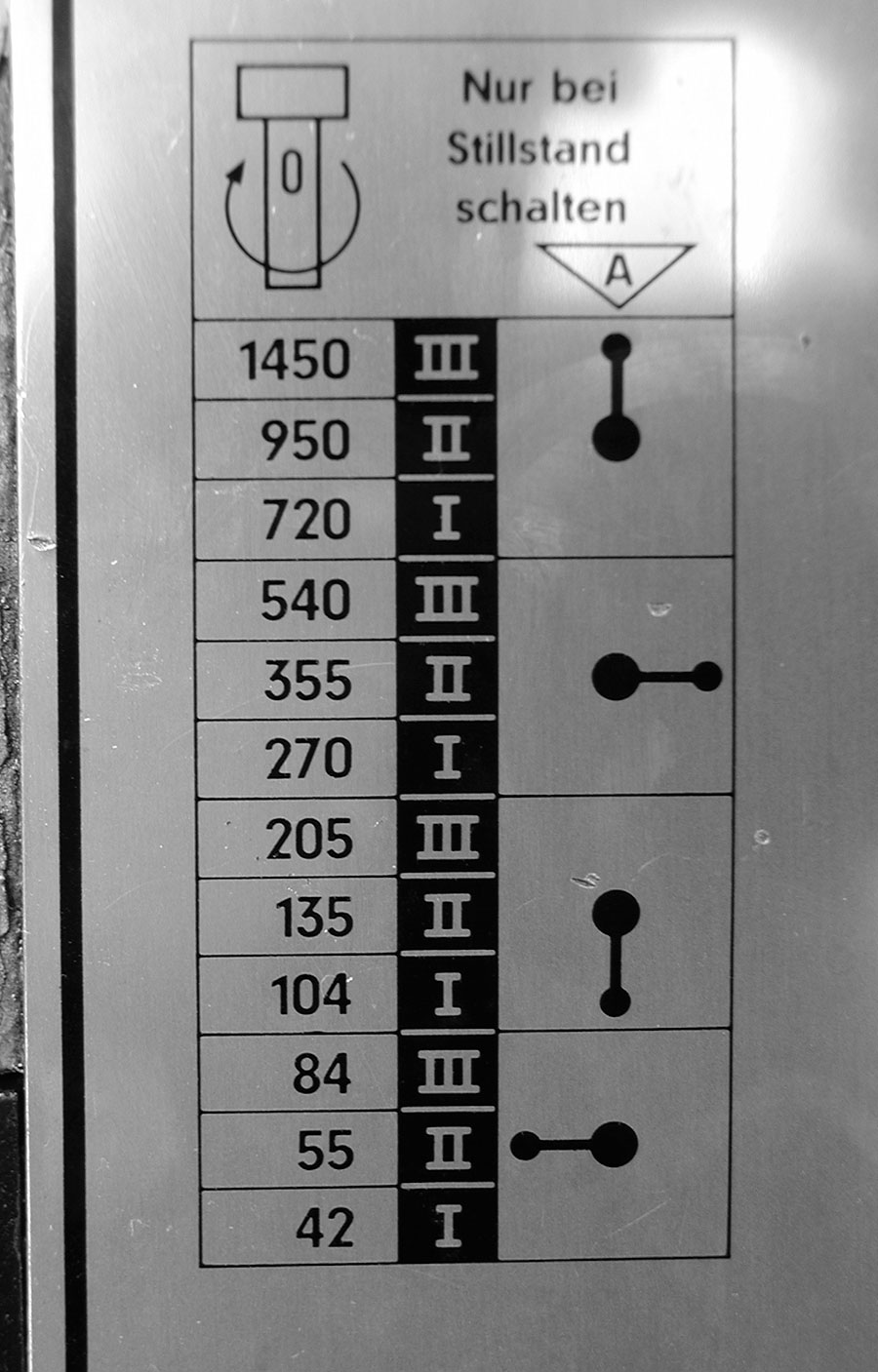
Vorschub
Ist die Drehzahl eingestellt, der Motor auf Touren und der Spiralbohrer eingespannt, muss das Bohrgerät noch ins Werkstück versenkt werden, damit sich überhaupt Späne zeigen und durch die Bude fliegen.
Zu diesem Zweck lassen sich hohlgebohrte Welle, Bohrfutter und Knethaken mittels Hebel hoch- und runterfahren. Mit einer Rückzugfeder versehen, erlaubt dieser Vorschubhebel sowohl gefühlvolles Anbohren als auch brutales Quälen von Bohrer und Werkstück. Dieser Hebel ist bei den allermeisten Maschinen rechts angebracht und erlaubt dem Maschinisten, mit der linken Hand den Schraubstock zu halten oder mit der Bohrwasser-Flasche herumzuplempen.
Verlangt die Bohrung nach einer bestimmten Tiefe, weil das Werkstück beispielsweise sonst einfach zu Ende ist, so kann man mit Tiefenanschlag bohren. Bei einer bestimmten Tiefe setzt das Ding auf und begrenzt weiteren Vortrieb. Weil größere Bohrungen auch große Vorschubkräfte erfordern können, müsste der Vorschubhebel indes bei großen Maschinen immer länger werden oder anders übersetzt sein. Als Lösung besitzen diese Maschinen einen automatischer Vorschub. Das ist ein einstellbares Extra-Getriebe, das am Hauptgetriebe dranhängt und die Bohrspindel mit einer definierten Geschwindigkeit und aller Gewalt absenkt.
Der Vorschub pro Spindelumdrehung lässt sich einstellen, so dass man als Herr der Späne bei laufender Leier nur den Vorschubhebel einlegt und für die Kühlung sorgen muss – die Maschine bohrt von selbst. Großer Nachteil dieses automatischen Vorschubs ist seine mangelnde Sensibilität. Das Ding bohrt und drückt, bis irgendein Spannstift abschert, sich das Bohrfutter spektakulär in den Tisch fräst oder der Schraubstock um den Bohrer kreist.
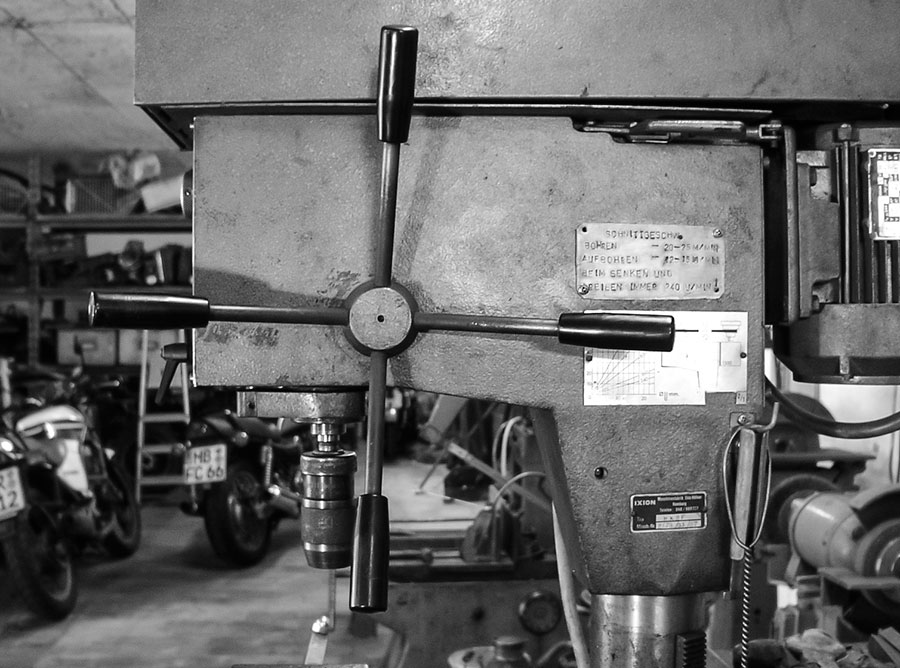

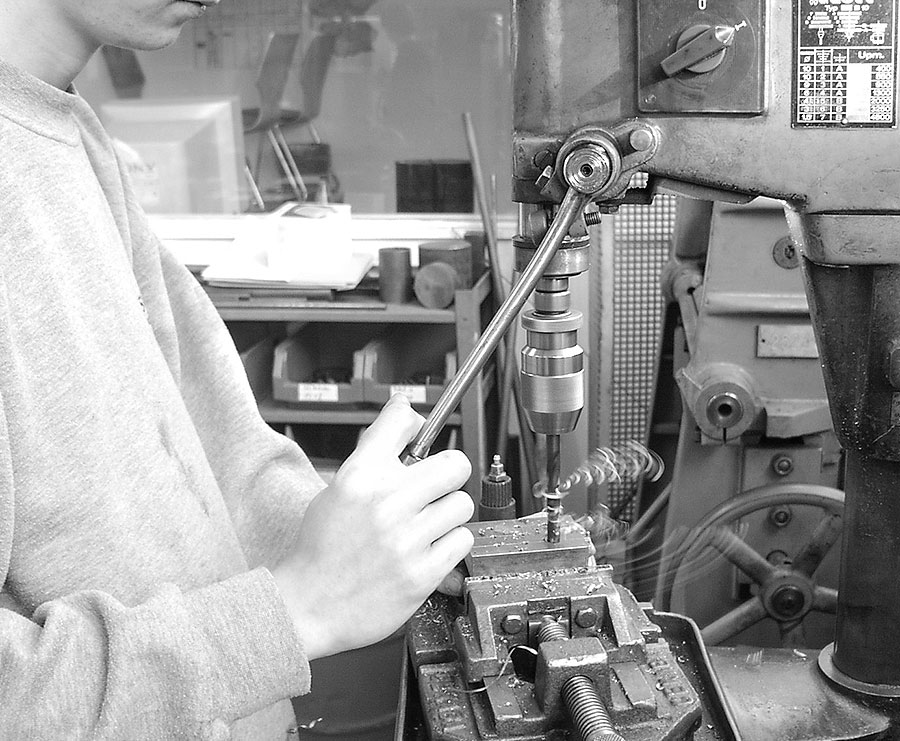
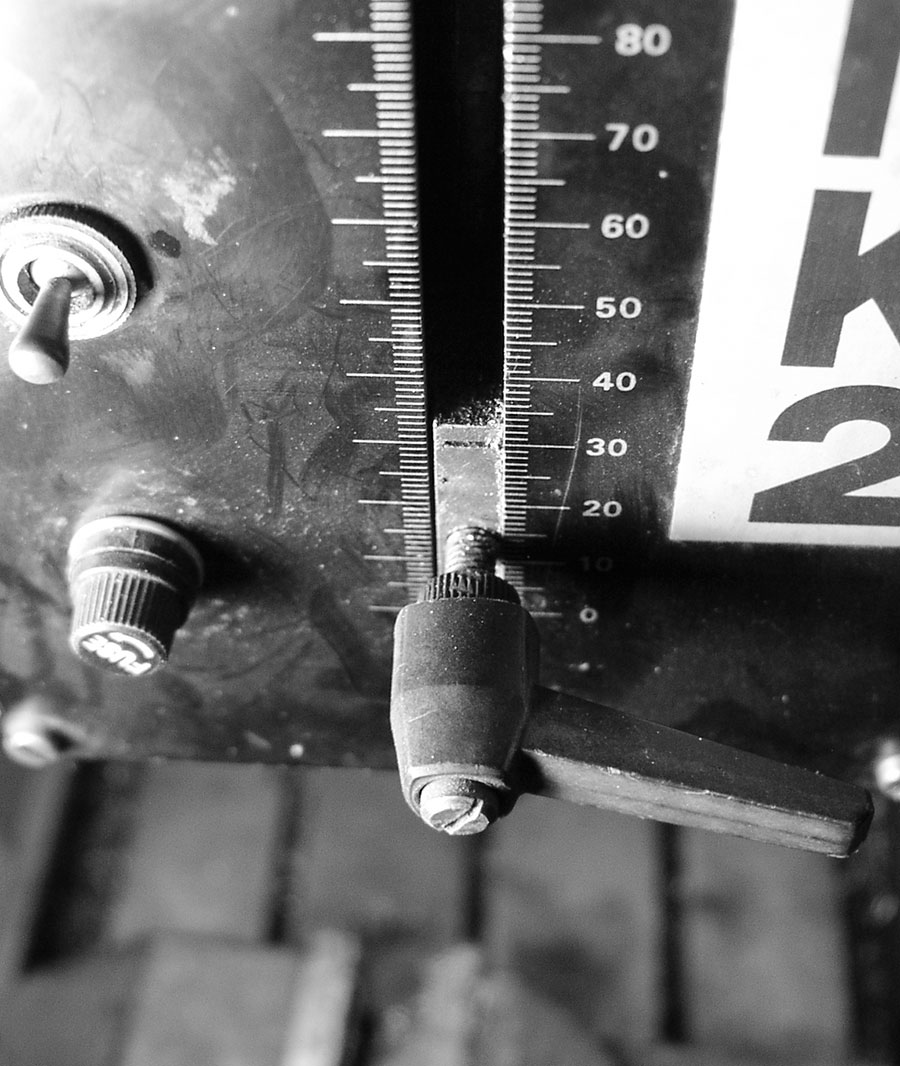
Letzte Aktualisierung am 2024-04-05 / Affiliate Links / Bilder von der Amazon Product Advertising API
Schraubstock, Tisch, Spannmittel
Zu einer Säulenbohrmaschine gibt es umfangreiches Zubehör, weil mit der nackten Maschine kaum etwas anzufangen ist. Utensil Nummer eins ist dabei der Schraubstock, in den man kleine Teile einspannt.
Je nach Qualität ist das ein eher günstiges Teil mit gegossenen Backen oder ein geschmiedetes Luxusmodell mit gefrästen und austauschbaren Backen. Das ist immer vorzuziehen, wenn es darum geht, Bohrungen wirklich winkeltreu anzubringen oder tiefe Gewinde sauber einzusetzen. In jedem Fall ist dieser Schraubstock das, was allermeist auf dem Tisch der Bohrmaschine liegt. Runtergenommen wird der Schraubstock nur, wenn größere Teile nicht zu spannen sind oder sie eine saubere Rückseite haben und leicht deshalb leicht zu bearbeiten sind.
Beim Bohren ohne Schraubstock besteht allerdings immer die Gefahr, auch den Schraubstock zu perforieren. Diese Kampfspuren an einer gebrauchten Maschine geben dem geneigten Käufer Aufschluss über die Laufleistung der Maschine. Ein zerbohrter Tisch, der Ähnlichkeit mit einem angebissenen Butterkeks hat, lässt also auf eine bewegte Vergangenheit schließen.
Um den Schraubstock auf dem Tisch zu fixieren oder große Teile mit Spannpratzen auf den Tisch zu schrauben, sind im Tisch immer T-Nuten zu finden. Mit passenden Nutensteinen lässt sich der Schraubstock so festknallen, dass mit einem Anschlag Serienbohrungen ein Klacks sind. Bei Bohrerdurchmessern von mehr als 10mm verhindert das Festschrauben überdies, dass die Maschine den Schraubstock herumreißt und nach Abbrechen des Bohrers auf den Perserteppich pfeffert. Mit diesem Spannzeug lassen sich aber noch ganz andere Sachen auf den Tisch spannen: das sind zum Beispiel Prismen oder Winkeltische, die die Anlagefläche des Werkstücks um 90° kippen.
Für anspruchsvolle Probleme gibt ́s sogenannte Teilköpfe, die Bohrungen gleichmäßig auf dem Umfang des Werkstücks verteilen können. Ebenfalls sehr lecker ist ein Kreuztisch, der sich auch auf den vorhandenen Tisch schrauben lässt. Mit ihm wird die Bohrmaschine zur Behelfs-Fräsbank. Er lässt sich in zwei Achsen verfahren und macht es möglich, Bohrungen auf wenige Hunderstel Millimeter genau zu positionieren oder kleine Fräsarbeiten sauber herzustellen.
All dieses Zubehör ist schön, teuer und wird so selten benötigt, dass man damit in aller Regel bis zum nächsten Sechser im Lotto wartet. Nicht warten sollte man indes mit dem Kauf von Bohrern, Senkern und anderem – die nächste Folge zeigt, was Not tut und wie es zum Einsatz kommt.




