Pressing pistons out of the saddle
Anyone who wants to undertake the honorable work of repairing a brake caliper must remove the piston from the saddle. On some models, this can be done almost automatically with a pair of water pump pliers. On the vast majority, however, it does not: in this case, the driver has understood “maintenance” to mean very long “servicing” and replaced the brake fluid 10 or more years ago. The piston is then caked in the brake calliper and can only be coaxed out of its rusty bed by force.
This force is typically applied by the fine man using compressed air so that the piston -flopp!- jumps out of the cylinder. During this procedure, the dust protection sleeve of the caliper usually remains intact and can be reused (if the repair kit has annoyingly been ordered incorrectly again). However, it is not so easy to get an unruly piston out of the saddle without compressed air – as a rule, you will either damage the sleeve or the collar of the piston, or both, when you use a pair of pliers.
There’s no need to mention the fact that it’s not even necessary to dismantle calipers that have seized up and that the pistons are simply pressed out using the brake pedal (if there’s no compressed air).
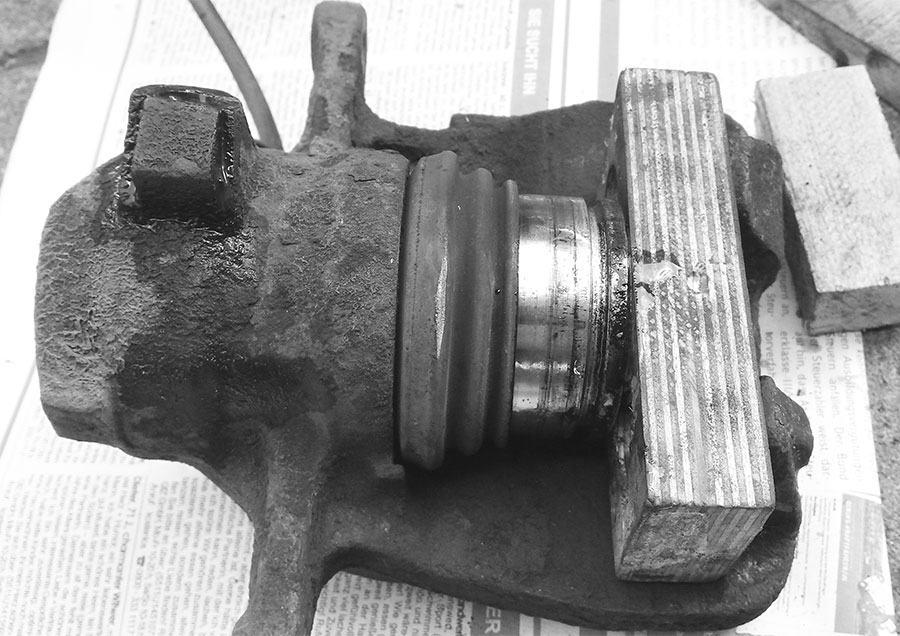
Build your own adapter
However, if the rusty lump of dirt with the piston fitted is already on the workbench, good advice is expensive. How do you get pressure onto the piston surface? After all, each of these greasy things contains a small hydraulic plunger that presses the grease from the cartridge into the hydraulic hose. Although the pressure of this does not come close to that of a vehicle brake system, it is enough to coax the sluggish piston out of the floating caliper.
The free end of an old brake hose, which already has the right thread for the brake calliper, is suitable as an adapter.
And all you need for the connection for the grease gun is a simple grease nipple.
The construction is therefore impressively simple: Saw off the brake hose, drill out the central hole to 4.2 millimeters and cut an M5 thread into the hole.
Then screw the grease nipple into the brand new adapter.
That’s it!
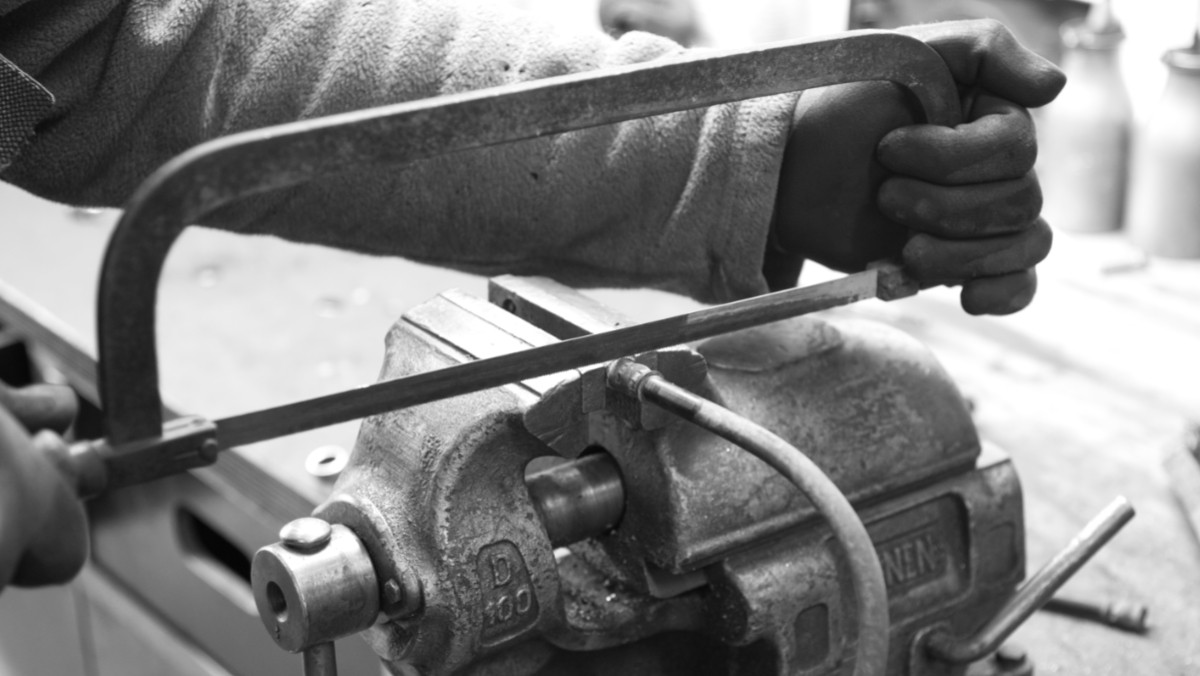
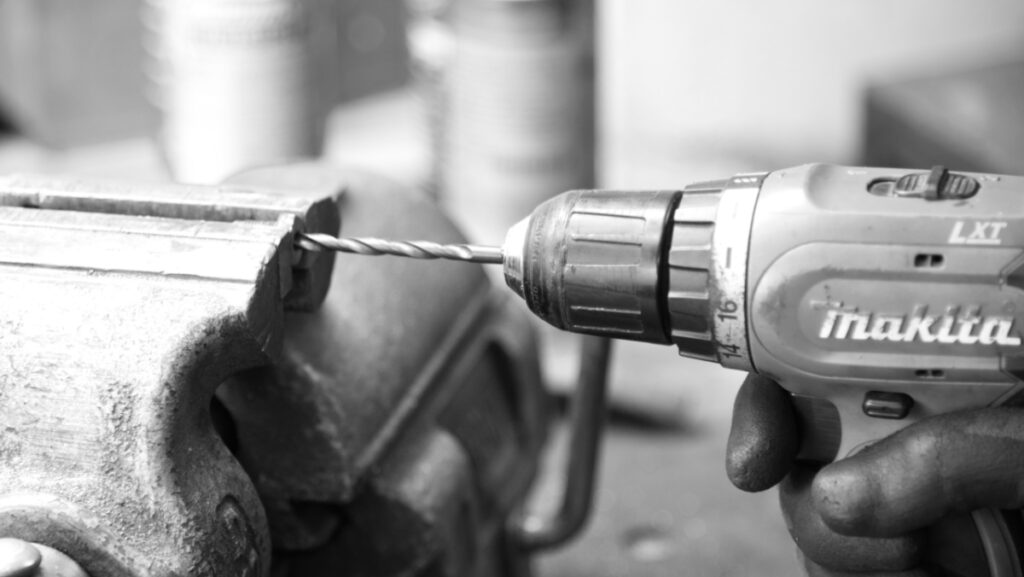
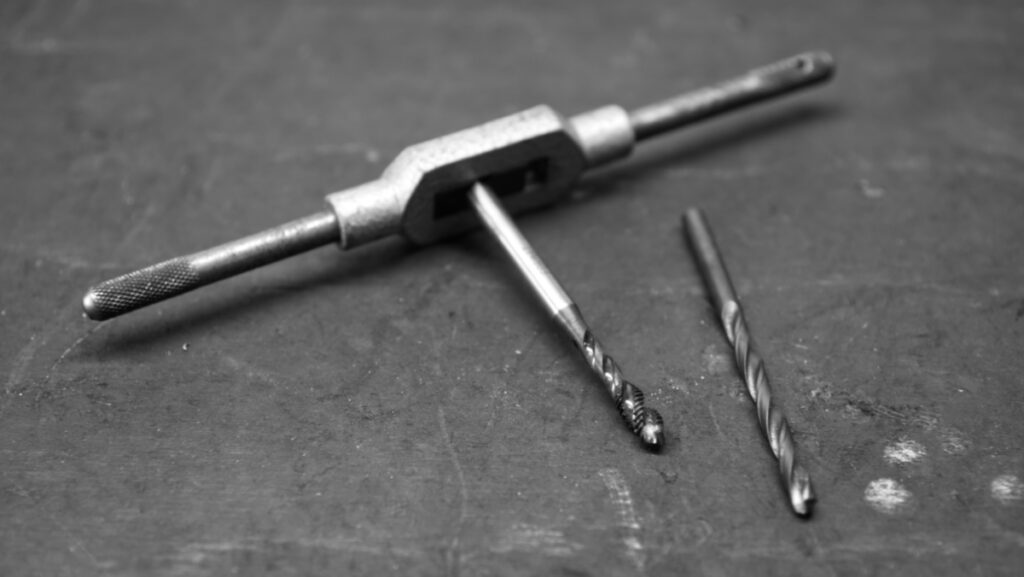
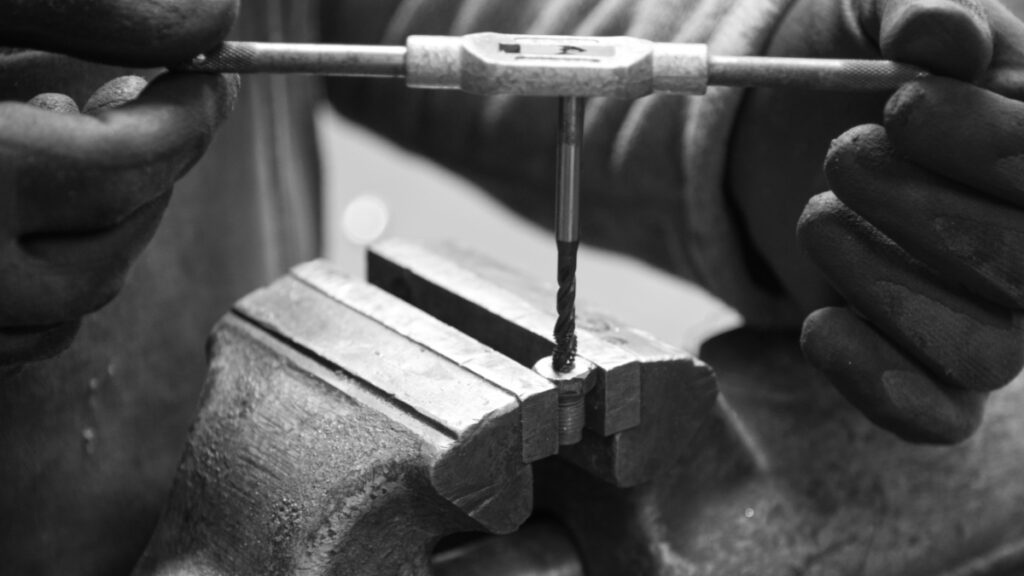
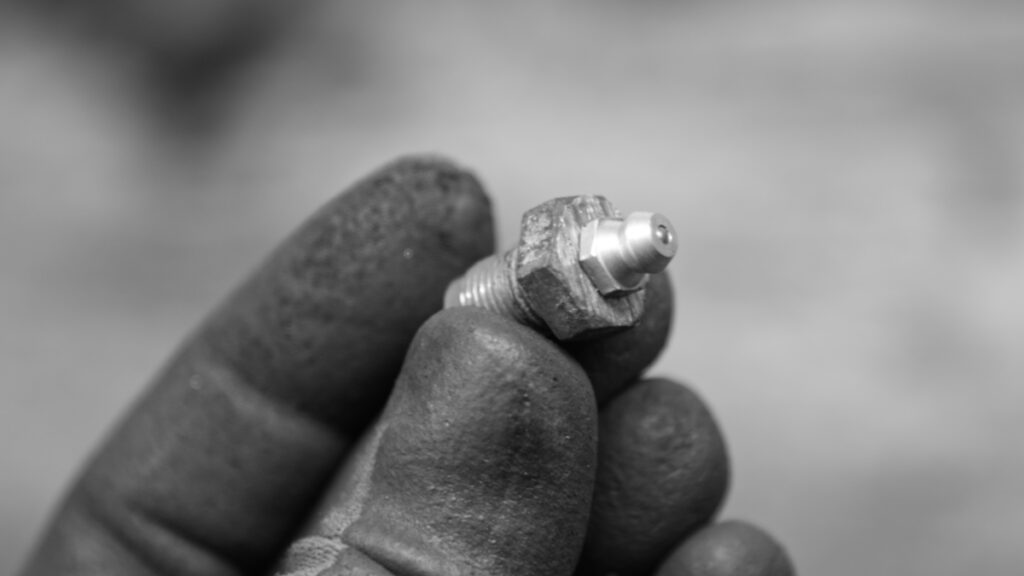
Press the brake piston out of the caliper
Freshly applied in the brake caliper, the adapter now transfers the grease from the press into the piston chamber. As a result, after just a few strokes on the greasy swivel, the unruly rotating part can only move in one direction and eventually ends up lying on the workbench.
Although this procedure costs valuable bearing grease, it is better than a crushed piston. And since the next time you are one of those who have to use a compressed air adapter or press the pistons out with the brake pedal, you can save the grease in an old tin can – and use it in years to come for the ball of the trailer coupling, for example. Helau!
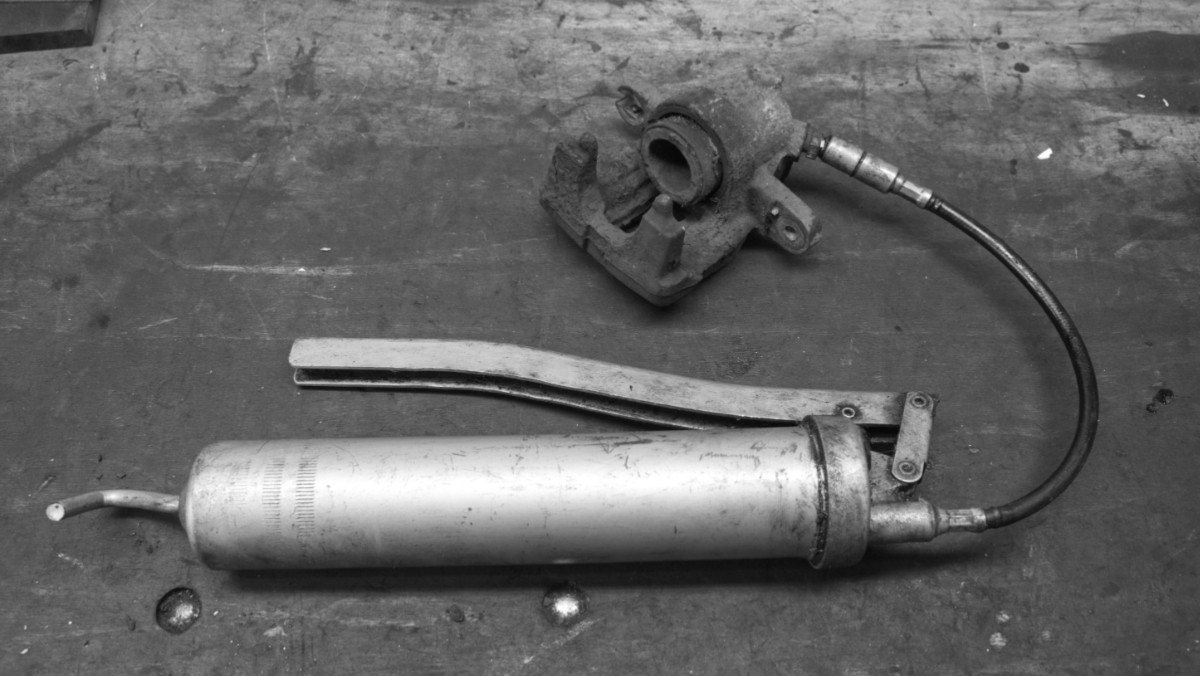
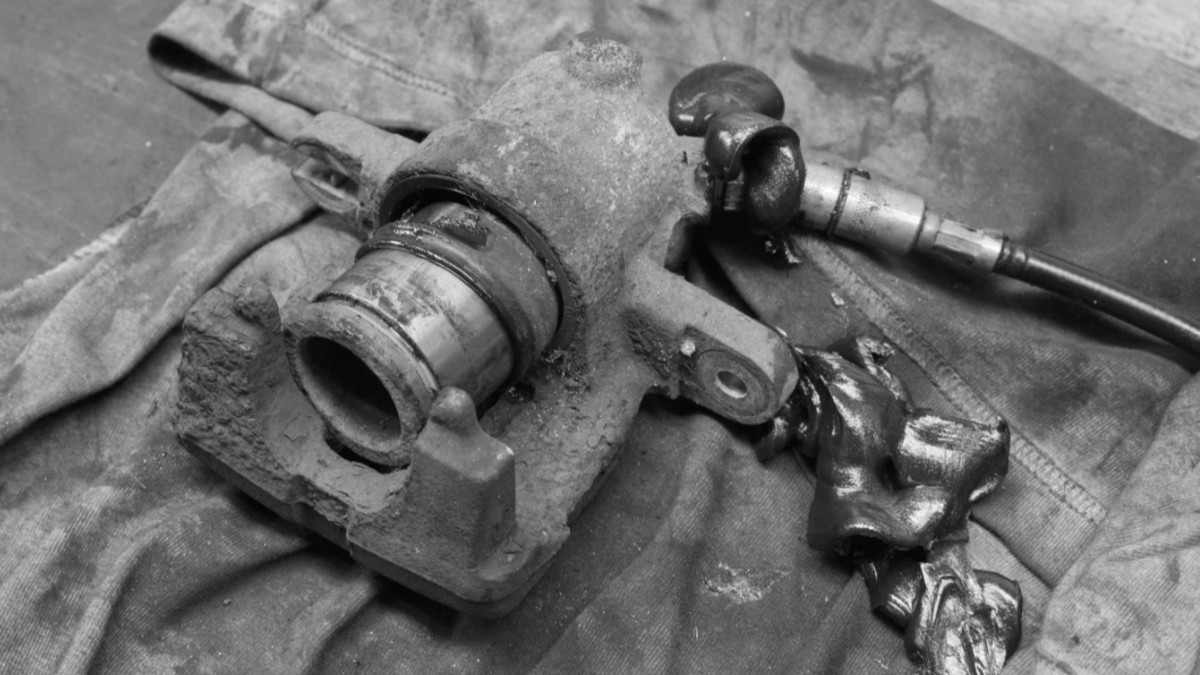