The idea of bracing two tapered roller bearings against each other and then using them as wheel bearings is as old as it is cheap. In principle, such a design consists only of a fixed axle stub onto which the brake drum or disk with the two bearings is pushed; the outer rings of the two bearings are pressed firmly into the rotating brake drum or disk. The inner rings and rolling elements rotate loosely between the stub axle and the outer ring; they are pressed together with a nut. And it is precisely this pressing together that logically defines the preload or adjustment of the two bearings.
That’s simple and good. But how exactly is the stupidest mechanic supposed to adjust such a construction without the bearing being too loose or too tight? At this point, the designer’s recently grayed hair falls out in clumps: Too loose an adjustment causes the bearing to wobble, too tight makes the bearing stiff. At both extremes, the rolling elements and bearing rings wear out either rapidly or even at record speed.
The solution consists of a thick adjusting washer that lies under the fine-thread adjusting nut. This washer not only serves as a washer for the nut. In fact, all contact surfaces are (coincidentally) dimensioned in such a way that they serve as a measuring instrument for the preload of the bearing.
This washer can therefore be moved sideways with a flat-blade screwdriver when the axial bearing pressure is correct. Oho! But what does “just barely” mean?
Of course, half a dozen questions immediately pop into the clever man’s head: Is all this junk lubricated? With which lubricant? How wide is the blade of the screwdriver? How high can the torque on its handle be?
Another ingenious feature of the design is the locking mechanism for the clamping or adjusting nut – it is secured against twisting with a locking plate and split pin. And as only three positions (360°/3 = 120°) are possible at this point, you have to decide between “too tight” and “too loose” at any intermediate position. Whew!
The adjustment of such bearings is therefore like everything else on earth: An eternal compromise. Once all components have been fully lubricated with grease, the pulley should not be too easy to move back and forth with a moderate turn of the screwdriver. On the other hand, it should not be nailed down. Above all, the mounted wheel must run really smoothly and must not be slowed down by the bearing. Of course, it must not wobble (at the other extreme) under any circumstances.
If you want to be on the safe side, make a little extra checkbox in your service booklet that also needs to be ticked off: check the preload of the wheel bearings. Even if the saying “it settles” has always been a fairy tale when it comes to wheel bearings, all parts wear out – and perhaps make a few degrees more on the adjusting nut possible in the coming year.
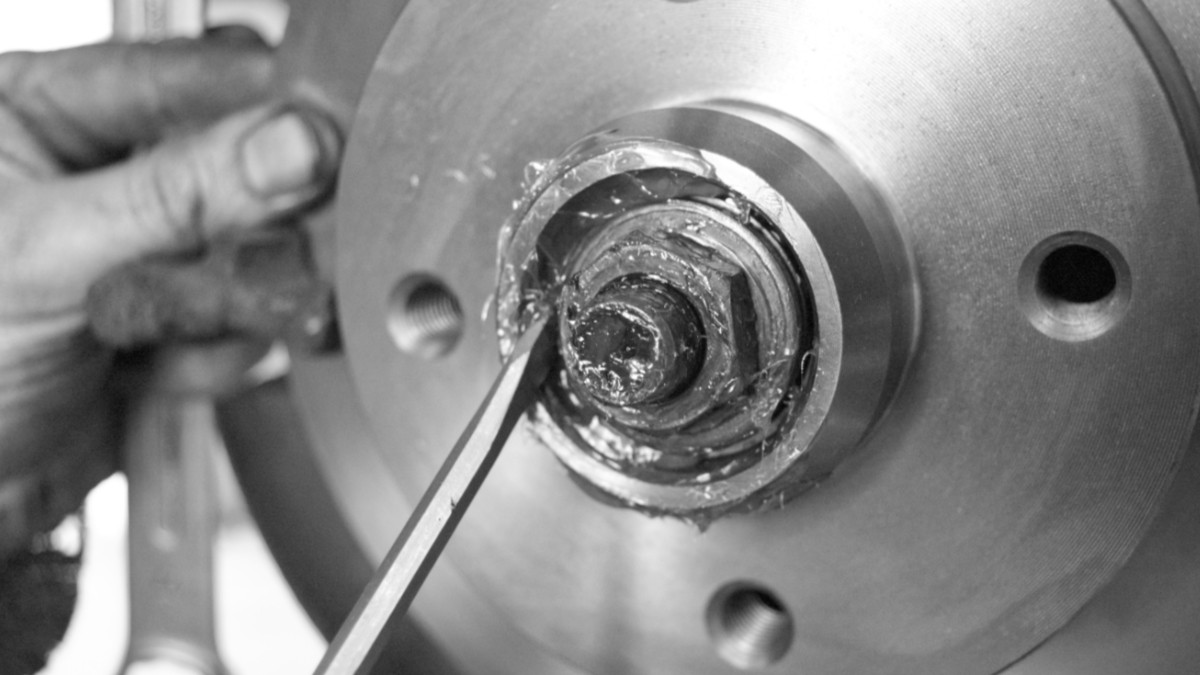