Foreword
A classic from the autoschrauber.de treasure trove from our esteemed colleague Boscho.
Even though complete exhaust systems now only cost the equivalent of two bunches of celery, a repair like this saves valuable resources and a trip to the parts store.
We apologize for the poor quality of the pictures – they were taken in 2002 with an Olympus 2020 and a gigantic 1.6 megapixels. Unfortunately, the original pictures have been lost. However, repairing old mufflers still works in exactly the same way.
Repair obsolete?
The third-hand diesel car suddenly sounds like a V8? Your beloved van sounds like a Russian tank in off-road gear? Clearly, the exhaust is leaking, and not just too badly. And if the MOT date is looming, there is an urgent need for action.
Those whose financial situation does not allow them to rush to their trusted parts dealer and beg for a new silencer can be helped with the tinkering described below.
All you need is a defective exhaust, sheet metal and a gas-shielded welder.
Since the rescue has something to do with welding, the exhaust is not always, but usually mounted under the car and it is quite unpleasant to be bitten on the neck by glowing welding spatter, the first thing to do is to get the pipe out! This is easier said than done, as the screw connections on the exhaust in particular tend to rot quite unpleasantly due to the strong heat fluctuations. Anything that doesn’t want to come apart is forcibly separated – hacksaws, angle grinders and nut splitters are the tools of choice here, sometimes simply a blowtorch and a little patience.
However, you should be careful with the blowtorch, otherwise you will suddenly have an enlightening experience with flaming underbody protection.
Advantage: the exhaust repair becomes obsolete because the car is burning down.
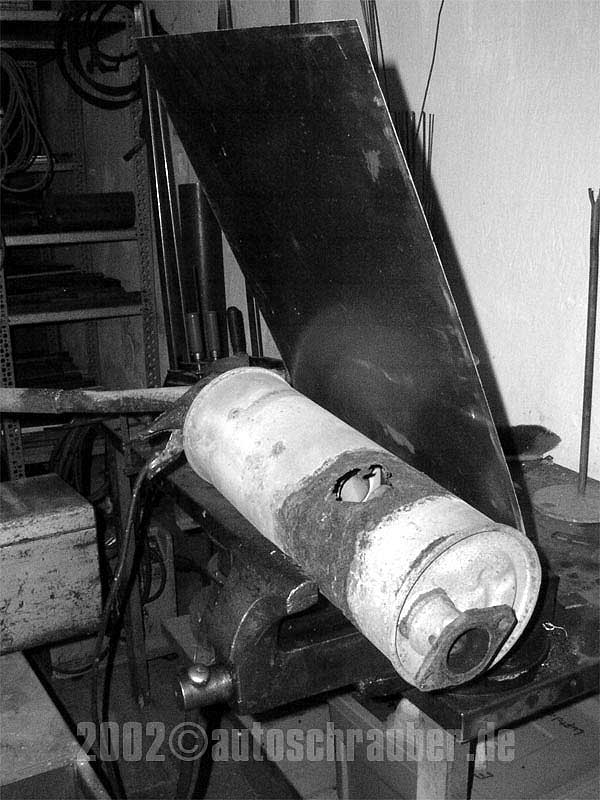
Hole in sheet metal
The pot is out and the car still exists? Then it’s worth taking a look at the muffler. If, in addition to a perforated shell, there is also massive corrosion on the inside, the only option is to throw the part on the scrap heap and buy a new one (whether that of an exhaust or a car is up to the individual’s economic calculation).
However, if there really is only a hole in the body panel, it can be easily (and MOT compliantly) repaired by putting a sheet metal jacket on the good piece. To do this, you first need sheet metal – standard bodywork sheet metal is just right.
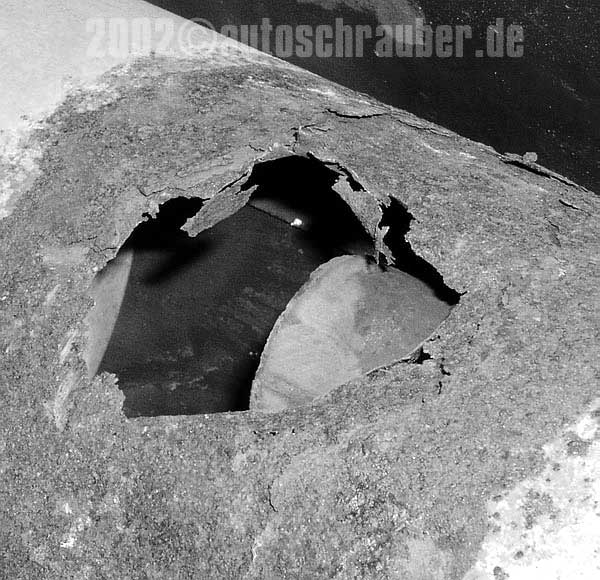
Tailor-made suit
This sheet metal is now used to make new clothes for the exhaust.
To do this, you should first check whether the muffler is cylindrical and not perhaps conical (difficult) or even curved (almost impossible).
The patch plate is then cut according to the measurement results.
This can be one or two millimeters narrower than the pot without the two “collars” at the ends; the gap is later closed with the weld seam.
A plate that is too wide, on the other hand, will be awkward because it cannot be guided and fixed properly.
To be able to weld properly, you need clean sheet metal – otherwise you can forget about it. Therefore, the longitudinal seam of the exhaust is now filed. The same is done to the sleeve on both flanges.
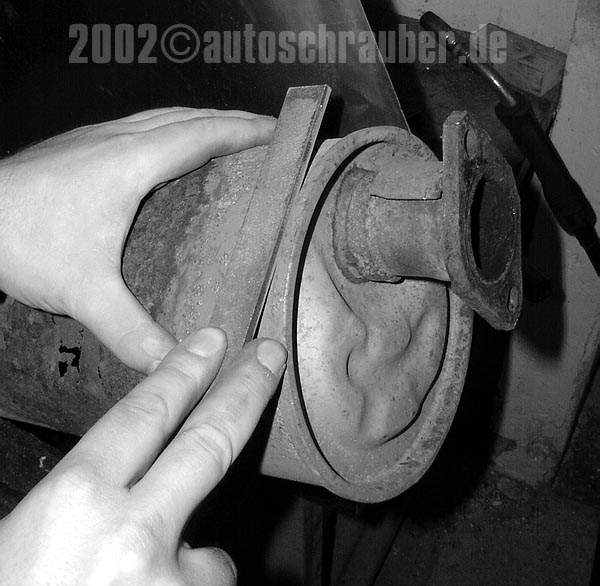
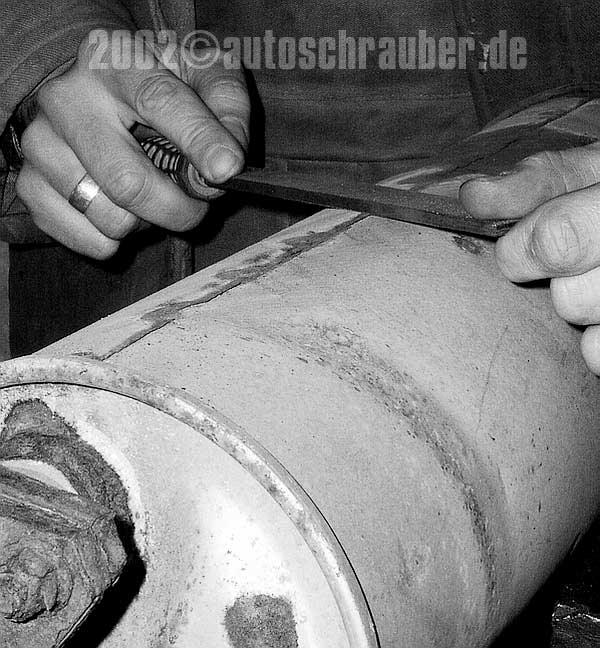
Point by point
When the metal shines bright, you can weld. First, the sheet metal is spot-welded to the longitudinal seam of the exhaust silencer. It is important to work cleanly and align the sheet metal precisely, because if you mess up here, everything will be crooked later on.
The metal sheet is then bent around the housing and dotted on the outside. A helper is not absolutely necessary, but definitely helpful. However, he will also help you drink your beer. Everyone has to set their own priorities…
When you get to the end, the sheet metal becomes a little unruly.
This doesn’t help, however, because exhaust pipe welders are really nasty and don’t shy away from brutality, so not only a screw clamp is used, but also a hammer.
If that doesn’t work, the next biggest hammer is used.
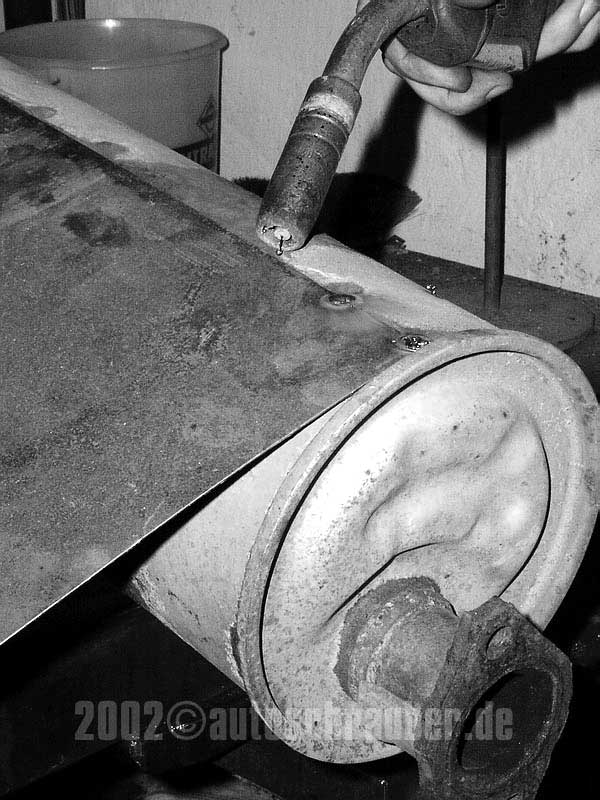
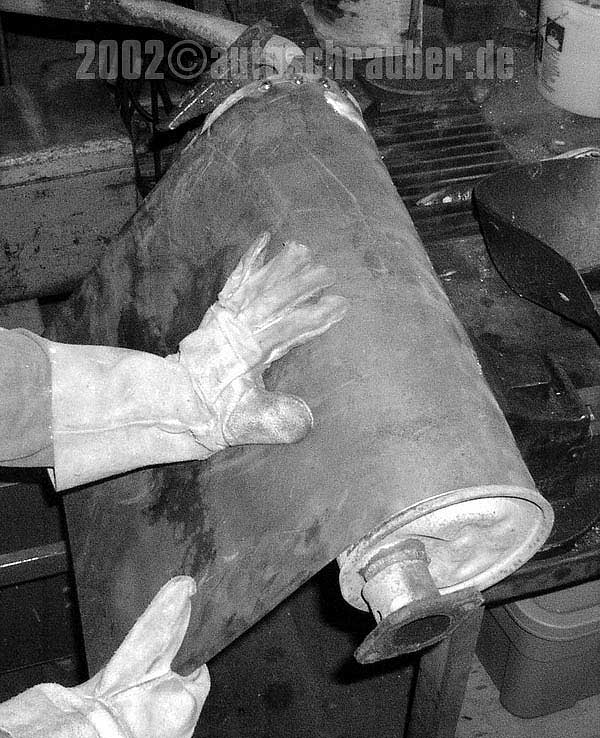
Letzte Aktualisierung am 2024-04-03 / Affiliate Links / Bilder von der Amazon Product Advertising API
Join the joint
If the sheet metal holds all around, you can and must weld through the seams. If not, the MOT guy will no longer see the hole – but he can still hear it.
When welding on the flanges, make sure that the torch is positioned on the flange, from where the weld pool is briefly drawn onto the sheet metal and then swung back onto the flange.
Remember: if you fry on the sheet metal for too long, you will burn a hole in it.
Which would be counterproductive; after all, we are trying to get such a hole tight.
As we are already welding so well, we go one better and re-weld the weld seams on the pipes, because they also tend to rot through.
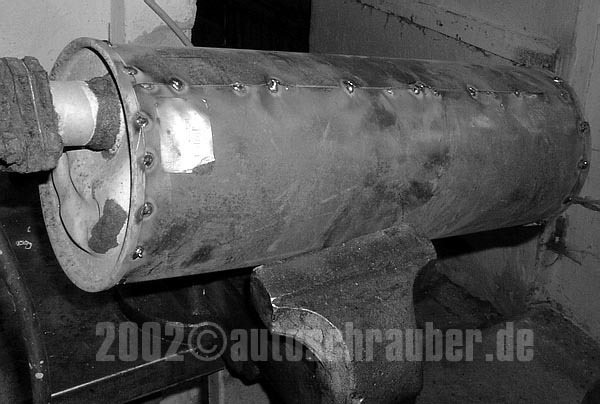
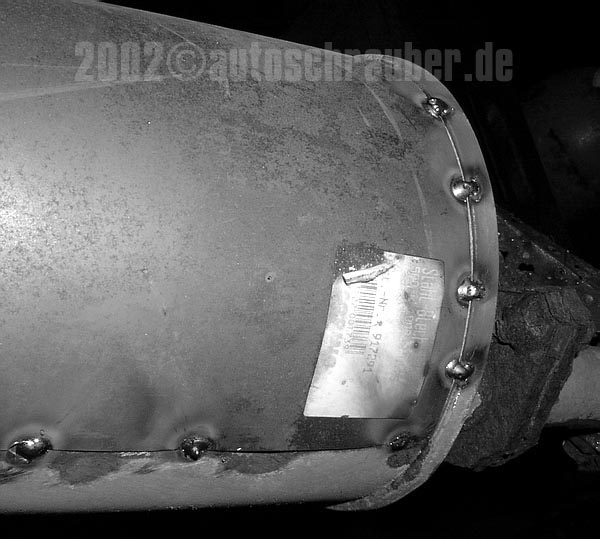
Final spurt
Done: the exhaust is tight again and can now be refitted.
If you want to do it some good, mist it with a little zinc spray. Untreated, however, it should also last another two years. And since we learned from our rich uncle that you need a new car every two years at the latest anyway, that’s more than enough.
And if the rest of the pipe has also been eaten away, we recommend our article on repairing dilapidated exhaust pipes.
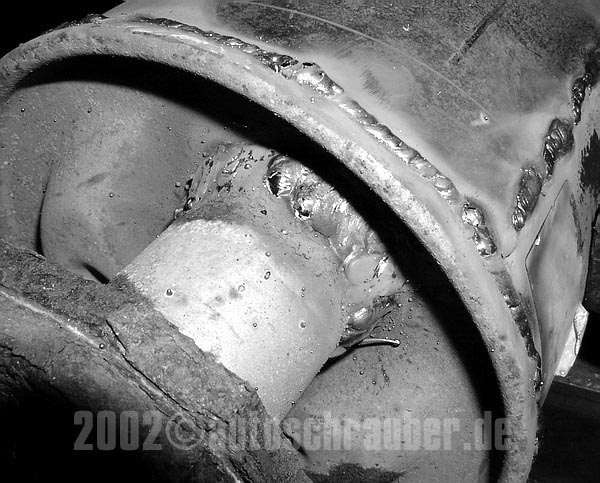